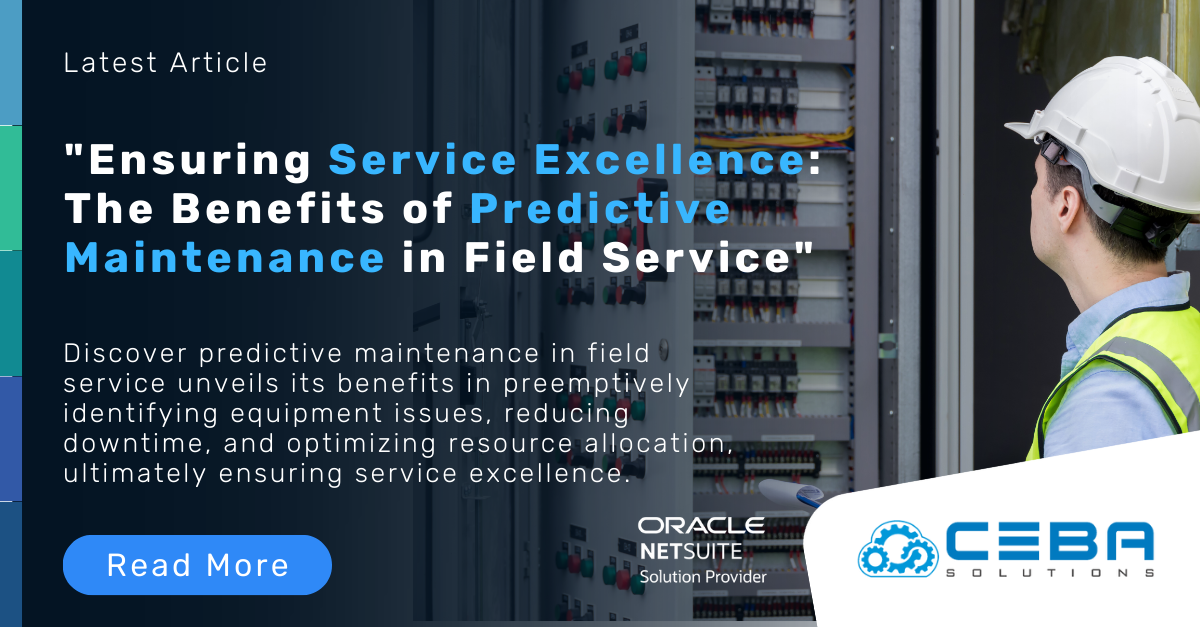
Ensuring Service Excellence: The Benefits of Predictive Maintenance in Field Service
Ensuring Service Excellence: The Benefits of Predictive Maintenance in Field Service
Predictive maintenance is revolutionizing field service management by transforming how maintenance tasks are scheduled and executed. This proactive approach uses data-driven insights to predict equipment failures before they occur, ensuring that maintenance is performed more efficiently and effectively. This article explores the numerous benefits of predictive maintenance, demonstrating how it can enhance service quality, reduce costs, and improve overall customer satisfaction.
1. Minimizing Unplanned Downtime
Overview of Predictive Maintenance
Predictive maintenance primarily aims to reduce unplanned downtime by identifying potential equipment failures before they result in actual breakdowns. By monitoring equipment conditions in real-time and analyzing data trends, predictive maintenance allows service teams to intervene preemptively.
Benefits:
Enhanced Reliability: Equipment is less likely to experience unexpected failures, leading to more reliable operation. This increased reliability ensures that customers experience fewer interruptions, enhancing their trust in the service provider. Regular, proactive maintenance also prevents minor issues from escalating into major problems, further increasing equipment uptime.
Increased Productivity: Reducing downtime ensures that operations continue smoothly, enhancing overall productivity for customers. This continuous operation is crucial for businesses that rely on consistent equipment performance to meet their operational goals. With less downtime, employees can focus on their core tasks without frequent disruptions, leading to higher efficiency and output.
Real-World Application:
Companies like Siemens use predictive maintenance to monitor their industrial equipment. By analyzing data from sensors and using AI algorithms, they can predict potential failures and perform maintenance before issues arise, significantly reducing downtime. This approach has allowed Siemens to maintain high levels of operational efficiency and customer satisfaction.
2. Extending Equipment Lifespan
Importance of Regular Maintenance
Regular maintenance is crucial for the longevity of any equipment. Predictive maintenance optimizes the timing of maintenance activities to prevent overuse and undue stress on components, thereby extending their operational life.
Benefits:
Cost Savings: Longer equipment lifespans mean lower costs over time as the need for frequent replacements is reduced. This cost-effectiveness is a significant advantage for businesses looking to maximize their return on investment. By reducing the frequency of equipment purchases, companies can allocate their budgets more efficiently and invest in other critical areas.
Sustainable Operations: Extending the life of equipment also means less waste and a smaller environmental footprint. Sustainability is increasingly important to customers and stakeholders, and predictive maintenance supports these goals. By minimizing waste and promoting the reuse of existing equipment, businesses can demonstrate their commitment to environmental responsibility.
Real-World Application:
General Electric (GE) implements predictive maintenance for their jet engines, which helps in extending the lifespan of critical components. This approach not only saves costs but also supports GE's commitment to sustainability by reducing waste. The extended lifespan of jet engines reduces the need for manufacturing new components, thereby conserving resources and energy.
3. Optimizing Maintenance Schedules
Using AI and Machine Learning
Predictive maintenance uses AI and machine learning to analyze historical data and make informed predictions about when maintenance should be performed. This allows organizations to create optimized maintenance schedules that are based not on a fixed interval but on actual equipment condition and performance.
Benefits:
Efficient Use of Resources: Maintenance resources are utilized only when necessary, reducing wasted effort and costs. This efficiency ensures that resources are available when they are most needed, improving overall operational effectiveness. Technicians can focus their efforts on equipment that genuinely needs attention, rather than performing routine checks on all machines.
Less Intrusive Maintenance: By scheduling maintenance based on need rather than routine, interventions are less disruptive to operations. This minimizes the impact on productivity and allows businesses to operate more smoothly. By performing maintenance during off-peak hours or scheduled downtimes, companies can avoid interrupting critical processes.
Real-World Application:
IBM’s predictive maintenance solutions help businesses like the London Underground optimize their maintenance schedules. By predicting when equipment needs attention, they can perform maintenance during off-peak hours, minimizing disruption to services. This approach ensures that the subway system remains operational and efficient, with minimal impact on commuters.
4. Reducing Maintenance Costs
Financial Impact of Predictive Maintenance
Predictive maintenance can significantly reduce the overall costs associated with maintaining equipment. By preventing catastrophic failures and optimizing maintenance schedules, companies can avoid costly repairs and minimize unnecessary maintenance activities.
Benefits:
Lower Repair Costs: Addressing issues before they escalate can prevent expensive repairs and replacements. Early intervention helps maintain the integrity of equipment and reduces the financial burden of major repairs. By catching problems early, companies can fix them with minimal parts and labor, avoiding more extensive and costly repairs later.
Decreased Maintenance Overhead: Streamlined maintenance requires fewer resources and less time, reducing overall operational costs. This efficiency translates into cost savings that can be reinvested into other areas of the business. By optimizing the use of personnel and materials, companies can achieve significant savings on maintenance expenses.
Real-World Application:
DHL uses predictive maintenance to manage their fleet of delivery vehicles. By monitoring vehicle health and predicting maintenance needs, they reduce repair costs and keep their fleet operational, ensuring timely deliveries and customer satisfaction. This proactive approach helps DHL maintain a reliable and cost-effective delivery service.
5. Improving Safety
Safety Benefits of Regular Maintenance
Regular and timely maintenance ensures that equipment operates safely, reducing the risk of accidents caused by equipment failure. Predictive maintenance enhances this aspect by ensuring that all potential risks are identified and addressed proactively.
Benefits:
Enhanced Worker Safety: Reduces the likelihood of accidents on the job, protecting employees. Safe working conditions are a top priority for any organization, and predictive maintenance supports this by preventing equipment-related incidents. By maintaining equipment in optimal condition, companies can create a safer work environment for their employees.
Compliance with Safety Regulations: Helps ensure that equipment meets industry safety standards, avoiding legal issues and fines. Regulatory compliance is critical for maintaining a business’s reputation and avoiding costly penalties. Predictive maintenance ensures that equipment is regularly inspected and maintained, meeting all required safety standards.
Real-World Application:
Oil and gas companies like Shell use predictive maintenance to enhance the safety of their drilling operations. By predicting and addressing potential equipment failures, they can prevent accidents and ensure compliance with stringent safety regulations. This proactive approach helps Shell maintain a safe and compliant operation, protecting both their employees and the environment.
Conclusion
Predictive maintenance represents a significant advancement in field service management, offering benefits that resonate through every aspect of service delivery. By adopting predictive maintenance, companies can ensure higher equipment reliability, lower maintenance costs, and improved customer satisfaction. As technology continues to advance, the scope and effectiveness of predictive maintenance will only increase, making it an essential strategy for any field service organization committed to excellence.
The future of field service lies in the adoption of predictive maintenance technologies. These tools not only enhance operational efficiency but also promote safety, sustainability, and customer satisfaction. As more organizations recognize the benefits, predictive maintenance will become the standard approach, driving a new era of excellence in field service management.
By embracing predictive maintenance, companies can transform their maintenance strategies, ensuring that they are always prepared for potential issues and able to maintain high levels of service quality. This forward-thinking approach not only benefits the organization but also builds stronger, more reliable relationships with customers, fostering long-term success in the field service industry.