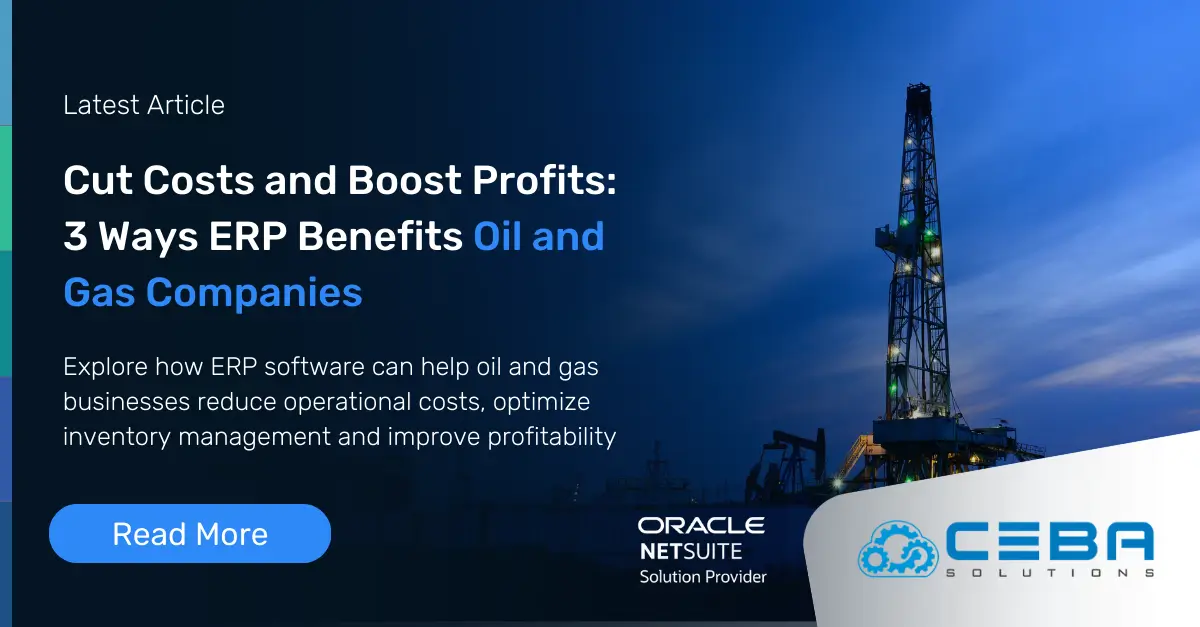
3 Ways ERP Can Help You Reduce Costs for Oil and Gas Field Service Businesses
3 Ways ERP Can Help You Reduce Costs for Oil and Gas Field Service Businesses
Did you know that in the competitive oil and gas field service industry, controlling costs is crucial for maintaining profitability and competitiveness? Enterprise Resource Planning (ERP) systems offer a comprehensive solution to help businesses streamline operations, optimize inventory management, and enhance workforce efficiency, leading to significant cost reduction opportunities. Here’s how:
Streamlined Inventory Management
Effective inventory management is crucial for controlling costs in oil and gas field services. ERP systems provide powerful tools to optimize this critical area, offering solutions that go beyond traditional inventory control methods.
Real-time Inventory Tracking
In the Oil and Gas Field Service Industry, advanced IoT technologies such as barcode scanning, RFID, and IoT sensors have revolutionized inventory management. These technologies provide field service providers with a comprehensive and real-time overview of equipment and materials, including availability, location, and status. Through continuous monitoring across multiple sites, managers gain intricate insights into inventory levels, allowing for precise decision-making. By leveraging IoT, field service companies can optimize inventory levels, reducing the need for excessive safety stock while ensuring the availability of critical equipment and supplies.
Predictive Maintenance
One of the most powerful features of modern ERP systems is their ability to implement predictive maintenance strategies. These systems collect and analyze data from various sources, including equipment sensors, historical maintenance records, and usage patterns and then use sophisticated machine learning algorithms to predict when equipment is likely to fail or require maintenance. This predictive capability allows businesses to schedule maintenance during planned downtime, dramatically reducing the occurrence of unexpected breakdowns and their associated costs. By ensuring that equipment receives timely maintenance, companies can extend the lifespan of their assets, deferring costly capital expenditures on new equipment and improving overall operational efficiency.
Automated Reordering
ERP systems bring a new level of intelligence to the reordering process. Again, by analyzing historical data and leveraging demand forecasting algorithms, these systems can determine optimal reorder points for each item in inventory. When inventory levels reach these predetermined points, the ERP automatically generates purchase orders, ensuring that new stock is ordered at precisely the right time to maintain optimal inventory levels. This automation significantly reduces the risk of human error in the ordering process and ensures that orders are placed consistently and efficiently. Similarly, by integrating with supplier systems, ERP can streamline the entire procurement process, from order placement to invoice payment, reducing administrative overhead and improving cash flow management.
Enhanced Workforce Management
In the oil and gas field service industry, efficient workforce management is critical to controlling costs and maintaining productivity. ERP systems offer a range of features that can significantly enhance workforce management, leading to substantial cost reductions and improved operational efficiency.
Optimized Scheduling
ERP systems bring a new level of sophistication to workforce scheduling. By leveraging advanced algorithms and real-time data, these systems can create optimized schedules that take into account a wide range of factors. These include employee skills, certifications, availability, location, and current workload, as well as job requirements, priority levels, and travel times.
This intelligent scheduling capability ensures that the right technicians are assigned to the right jobs at the right time. As a result, businesses can minimize overtime costs by more efficiently distributing work across their workforce. It also reduces idle time between jobs, improving overall productivity.This optimized scheduling can lead to reduced travel times and fuel costs, as technicians are assigned to jobs in a more geographically efficient manner.
Mobile Workforce Solutions
Modern ERP systems extend their functionality to the field through mobile applications, empowering techs to collect and complete job details in the field, rather than having to return to the office to complete administrative tasks. They can view job details, update work orders, log time and materials used, and even process payments, all from their mobile devices.
This real-time connectivity significantly reduces administrative overhead and improves data accuracy. It eliminates the need for paper-based processes and manual data entry, reducing errors and saving time. Technicians can also access important information such as equipment manuals, safety protocols, and customer history while on-site, improving their ability to complete jobs efficiently and effectively.
Skills-based Assignment
ERP systems maintain detailed profiles of each technician's skills, certifications, and experience. This information is used to match technicians with job requirements automatically. By ensuring that the most appropriately skilled technician is assigned to each job, businesses can significantly improve their first-time fix rates.
Higher first-time fix rates have a cascading positive effect on costs. They reduce the need for repeat visits, saving on travel costs and technician time. They also improve customer satisfaction, potentially leading to increased customer retention and positive word-of-mouth referrals, indirectly contributing to cost reduction by lowering customer acquisition costs.
Time and Attendance Tracking
ERP systems automate the time and attendance tracking process, eliminating the need for manual timesheets and reducing the administrative burden of payroll processing. Technicians can clock in and out directly through mobile apps, with GPS verification ensuring accuracy.
This automation saves time and improves the accuracy of payroll calculations, reducing errors and potential disputes. It gives managers real-time visibility into labor costs, allowing them to make informed decisions about overtime and resource allocation.
"In the oil and gas field service industry, ERP systems transform how companies manage inventory and workforce, significantly reducing costs and improving efficiency. These systems enable precise inventory tracking, predictive maintenance, and optimized workforce scheduling." - Zabe Siddique, CEO - CEBA Solutions
Data-Driven Decision Making
Being able to make informed decisions based on accurate, real-time data can significantly impact cost-reduction efforts. ERP systems are especially good at facilitating data-driven decision-making by providing a single source of truth for all operations and finance-related data as well as having advanced analytics capabilities, improved compliance management, and detailed project cost tracking.
Centralized Data Repository
One of the most powerful features of ERP systems is their ability to consolidate data from various departments and functions into a single, unified database. This centralization eliminates data silos that often exist in organizations, where different departments maintain separate databases that don't communicate with each other.
In an oil and gas field service context, this means that data from operations, finance, human resources, inventory management, and customer service are all integrated into one system. This integration provides a holistic view of the entire business, enabling managers to see how different aspects of the operation interact and affect each other.
The centralized data repository also significantly reduces the time and effort required for data reconciliation. Instead of manually compiling reports from different systems, which can be time-consuming and prone to errors, managers can generate comprehensive reports with a few clicks. This not only saves time but also ensures that all decisions are based on the most up-to-date and accurate information available.
Advanced Analytics
ERP systems don't just store data; they also provide tools for analyzing it. These advanced analytics capabilities allow businesses to derive meaningful insights from their vast amounts of data, identifying patterns, trends, and correlations that might not be apparent through manual analysis.
For oil and gas field service businesses, these analytics can reveal opportunities for cost savings that might otherwise go unnoticed. For example, the system might identify patterns in equipment failures, allowing for more effective predictive maintenance strategies. It could highlight inefficiencies in route planning for field technicians, leading to optimized schedules and reduced fuel costs.
Real-time dashboards and reports provide managers with up-to-the-minute information on key performance indicators (KPIs). This immediate access to critical data enables faster, more informed decision-making. Managers can quickly identify areas that are underperforming and take corrective action before small issues escalate into significant, costly problems.
Compliance Management
The oil and gas industry is heavily regulated, and non-compliance can result in hefty fines and operational disruptions. ERP systems can play a crucial role in managing compliance effectively and efficiently.
These systems can automate much of the compliance reporting process, ensuring that all necessary documentation is completed accurately and submitted on time. They can track regulatory requirements and automatically notify relevant personnel when actions are needed to maintain compliance.
ERP systems automatically maintain detailed audit trails of all transactions and activities. This comprehensive record-keeping is invaluable during audits, making it easier to demonstrate compliance and reducing the time and stress associated with regulatory inspections.
By streamlining compliance management, ERP systems not only reduce the risk of costly fines and penalties but also minimize the administrative overhead associated with regulatory compliance. This allows businesses to allocate more resources to core operational activities, indirectly contributing to cost reduction.
Project Cost Tracking
For oil and gas field service businesses, accurate project cost tracking is essential for maintaining profitability. ERP systems provide real-time visibility into all aspects of project costs, from labor and materials to equipment usage and overhead allocation. This granular level of cost tracking allows project managers to identify cost overruns quickly and take corrective action. They can see exactly where money is being spent and compare actual costs against budgeted amounts in real-time. This immediate feedback loop enables more proactive cost management, preventing small overruns from ballooning into significant financial losses.
Detailed cost data can also highlight areas where efficiency improvements can be made. For instance, it might reveal that certain types of equipment are more cost-effective to rent than to own, or that specific processes consistently run over budget and need to be re-evaluated.
Final Thoughts
ERP systems offer numerous benefits for oil and gas field service companies, from improved operational efficiency and reduced costs to enhanced compliance management and data-driven decision-making. By leveraging the power of ERP technology, businesses can gain a competitive edge and position themselves for long-term success in an increasingly competitive market.
If your oil and gas field service company is looking to streamline your operations, improve profitability, and gain a competitive advantage, we invite you to reach out to CEBA Solutions. Our team of experts has extensive experience implementing ERP solutions specifically tailored to the needs of the oil and gas industry. Contact us today to schedule a consultation and learn how CEBA Solutions can help you unlock the full potential of your field service operations.