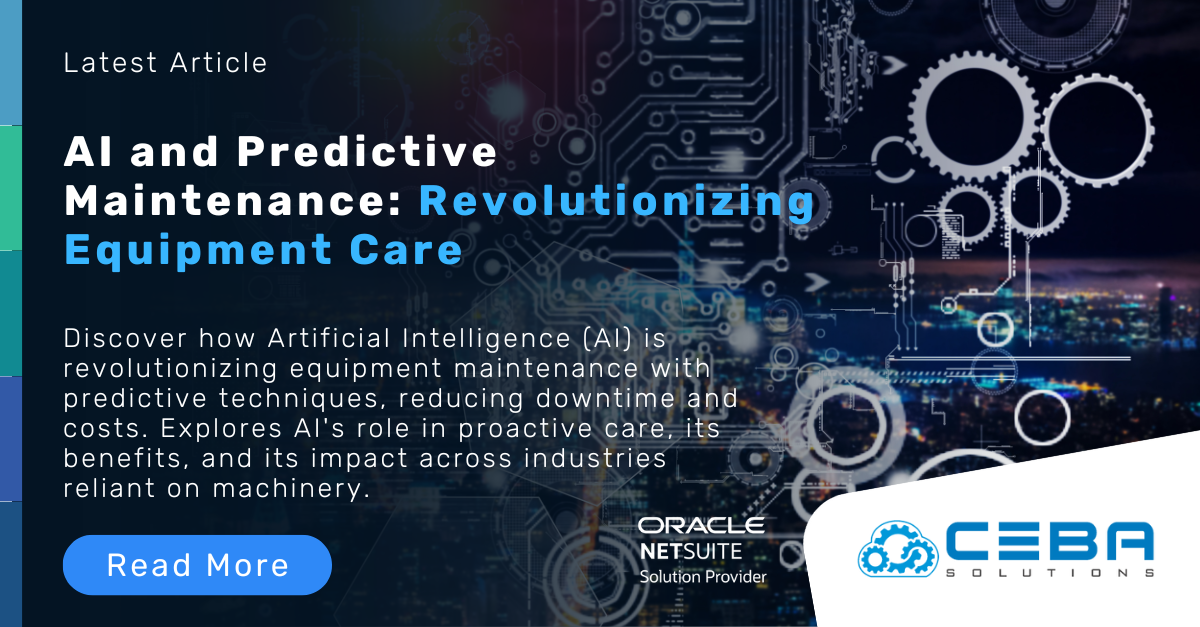
AI and Predictive Maintenance: Revolutionizing Equipment Care
AI and Predictive Maintenance: Revolutionizing Equipment Care
In today’s industrial and manufacturing landscapes, the maintenance of equipment is a critical aspect of ensuring operational efficiency, minimizing downtime, and reducing costs. Traditional maintenance strategies, such as reactive and preventive maintenance, often fall short in optimizing equipment care and performance. However, the advent of artificial intelligence (AI) and predictive maintenance is revolutionizing how businesses manage their equipment. By leveraging AI, companies can predict equipment failures before they occur, enabling proactive maintenance that enhances reliability and efficiency. This article explores how AI-driven predictive maintenance is transforming equipment care and the benefits it brings to various industries.
Understanding Predictive Maintenance
Predictive maintenance (PdM) is a proactive approach that uses data analysis tools and techniques to detect anomalies and predict equipment failures. Unlike preventive maintenance, which follows a scheduled timetable, predictive maintenance relies on the actual condition of the equipment. AI enhances PdM by analyzing vast amounts of data from sensors and other sources to predict when maintenance should be performed. This approach ensures maintenance is only conducted when necessary, preventing unexpected failures and extending the lifespan of equipment.
The Role of AI in Predictive Maintenance
AI plays a crucial role in predictive maintenance by utilizing machine learning algorithms, data analytics, and real-time monitoring to provide actionable insights. Here are key components of AI-driven predictive maintenance:
Data Collection and Integration
Sensors and IoT Devices: AI-driven PdM systems rely on data collected from various sensors and Internet of Things (IoT) devices installed on equipment. These sensors monitor parameters such as temperature, vibration, pressure, and humidity in real-time. The continuous flow of data from these sensors provides a detailed and dynamic picture of equipment health, allowing for timely interventions.
Data Integration: Integrating data from different sources, including historical maintenance records, operational data, and environmental conditions, provides a comprehensive view of equipment health. This holistic approach ensures that all relevant factors are considered when predicting equipment performance and potential failures.
Machine Learning Algorithms
Anomaly Detection: Machine learning algorithms analyze data to detect anomalies and deviations from normal operating conditions. These algorithms can identify patterns that indicate potential failures, enabling maintenance teams to address issues before they escalate. By continuously learning from new data, these algorithms become increasingly accurate over time.
Predictive Modeling: AI models are trained on historical data to predict future equipment failures. These models continuously learn and improve their accuracy over time, adapting to changing conditions and new data inputs. Predictive modeling helps in forecasting failure timelines and planning maintenance activities more effectively.
Real-Time Monitoring and Analysis
Continuous Monitoring: AI systems continuously monitor equipment in real-time, providing up-to-date insights into its condition. This allows for immediate detection of issues as they arise, ensuring that corrective actions can be taken promptly to prevent downtime.
Advanced Analytics: AI-driven analytics tools process and analyze data to provide actionable insights. These tools can identify root causes of issues, predict failure timelines, and recommend maintenance actions. Advanced analytics help in making informed decisions that enhance equipment performance and reliability.
Benefits of AI-Driven Predictive Maintenance
Reduced Downtime and Increased Reliability
Proactive Maintenance: By predicting equipment failures before they occur, AI-driven PdM allows for proactive maintenance. This reduces unplanned downtime and ensures equipment operates reliably, maintaining production schedules and minimizing disruptions.
Extended Equipment Lifespan: Timely maintenance based on actual equipment conditions helps extend the lifespan of assets, reducing the need for costly replacements. Regular and precise maintenance ensures that equipment remains in optimal condition, enhancing its longevity.
Cost Savings
Optimized Maintenance Schedules: Predictive maintenance ensures that maintenance activities are performed only when necessary, reducing unnecessary maintenance costs. This approach eliminates the inefficiencies of time-based maintenance schedules.
Lower Repair Costs: Early detection of issues allows for minor repairs before they escalate into major failures, reducing repair costs. Addressing problems in their early stages prevents expensive and extensive repairs.
Enhanced Safety and Compliance
Improved Safety: Predictive maintenance helps identify potential safety hazards before they lead to accidents, enhancing workplace safety. Ensuring equipment is well-maintained reduces the risk of malfunctions that could harm workers.
Regulatory Compliance: AI-driven PdM systems can help ensure compliance with industry regulations and standards by maintaining equipment in optimal condition. Compliance with safety and environmental regulations is easier to achieve with regular, condition-based maintenance.
Data-Driven Decision Making
Actionable Insights: AI provides actionable insights that enable data-driven decision-making. Maintenance teams can prioritize tasks, allocate resources effectively, and make informed decisions based on real-time data and predictive analytics.
Performance Optimization: Continuous monitoring and analysis of equipment performance help identify areas for optimization, improving overall operational efficiency. Data-driven insights guide improvements that enhance productivity and reduce waste.
Implementing AI-Driven Predictive Maintenance
Assessing Readiness and Setting Objectives
Readiness Assessment: Evaluate the current state of your equipment, data infrastructure, and maintenance processes. Assess readiness for implementing AI-driven PdM by identifying gaps and opportunities for improvement.
Clear Objectives: Define clear objectives for the predictive maintenance program, such as reducing downtime, lowering maintenance costs, and improving equipment reliability. Clear goals provide direction and measurable targets for the program.
Deploying Sensors and IoT Devices
Sensor Installation: Install sensors and IoT devices on critical equipment to collect real-time data. Ensure sensors are calibrated and provide accurate readings to gather reliable data for analysis.
Data Connectivity: Establish robust data connectivity to ensure seamless data transfer from sensors to the AI system. Reliable data transmission is essential for real-time monitoring and analysis.
Building and Training AI Models
Data Collection: Collect historical and real-time data to train AI models. Ensure data quality and completeness to build accurate and reliable predictive models.
Model Training: Use machine learning algorithms to train predictive models. Continuously update and refine models with new data to improve accuracy and adaptability.
Integrating with Existing Systems
System Integration: Integrate the AI-driven PdM system with existing maintenance management systems, enterprise resource planning (ERP) systems, and other relevant platforms. Seamless integration ensures that AI insights are actionable within the existing workflow.
User Interface: Develop user-friendly interfaces that provide maintenance teams with easy access to insights and recommendations. Intuitive interfaces enhance usability and adoption.
Training and Change Management
Employee Training: Train maintenance personnel on using AI-driven PdM tools and interpreting the insights provided. Emphasize the importance of data-driven decision-making and the benefits of AI.
Change Management: Implement change management strategies to ensure smooth adoption of the new PdM system. Address any resistance and highlight the benefits of predictive maintenance to gain buy-in from all stakeholders.
Continuous Improvement and Monitoring
Performance Metrics: Establish key performance indicators (KPIs) to monitor the effectiveness of the predictive maintenance program. Common KPIs include mean time between failures (MTBF), maintenance costs, and downtime reduction.
Regular Reviews: Conduct regular reviews of the PdM system’s performance and make necessary adjustments. Continuously seek opportunities for improvement to maintain and enhance the system's effectiveness.
Challenges and Considerations
Data Quality and Management
Data Accuracy: Ensure that the data collected is accurate, reliable, and representative of actual equipment conditions. High-quality data is crucial for effective predictive maintenance.
Data Volume: Manage the large volumes of data generated by sensors and IoT devices. Implement data storage and processing solutions that can handle big data efficiently.
Initial Costs and ROI
Upfront Investment: Be prepared for the initial costs associated with implementing AI-driven PdM, including sensors, data infrastructure, and AI tools. Investing in these technologies is essential for long-term benefits.
Long-Term ROI: Focus on the long-term return on investment, considering the cost savings, reduced downtime, and increased equipment lifespan that AI-driven predictive maintenance can deliver.
Integration and Interoperability
Seamless Integration: Ensure that the AI-driven PdM system integrates seamlessly with existing maintenance and operational systems. Address any interoperability issues to avoid data silos and ensure smooth data flow.
Vendor Collaboration: Work closely with technology vendors to customize AI solutions that meet your specific needs and address industry-specific challenges.
Security and Privacy
Data Security: Implement robust cybersecurity measures to protect sensitive data collected from equipment and sensors. Ensure that data is encrypted and access is controlled to prevent unauthorized access.
Privacy Compliance: Ensure compliance with data privacy regulations and standards. Address any concerns related to data collection and usage to maintain trust and regulatory compliance.
Conclusion
AI-driven predictive maintenance is revolutionizing equipment care by providing advanced solutions that enhance reliability, reduce costs, and improve operational efficiency. By leveraging machine learning algorithms, real-time data analysis, and predictive modeling, businesses can transition from reactive and preventive maintenance strategies to proactive maintenance. Implementing AI-driven PdM requires careful planning, data integration, and employee training, but the benefits far outweigh the challenges. As AI technology continues to evolve, its impact on equipment maintenance will only grow, driving innovation and excellence across various industries. Embracing AI for predictive maintenance is not just a competitive advantage but a necessary step toward achieving long-term operational success and sustainability.