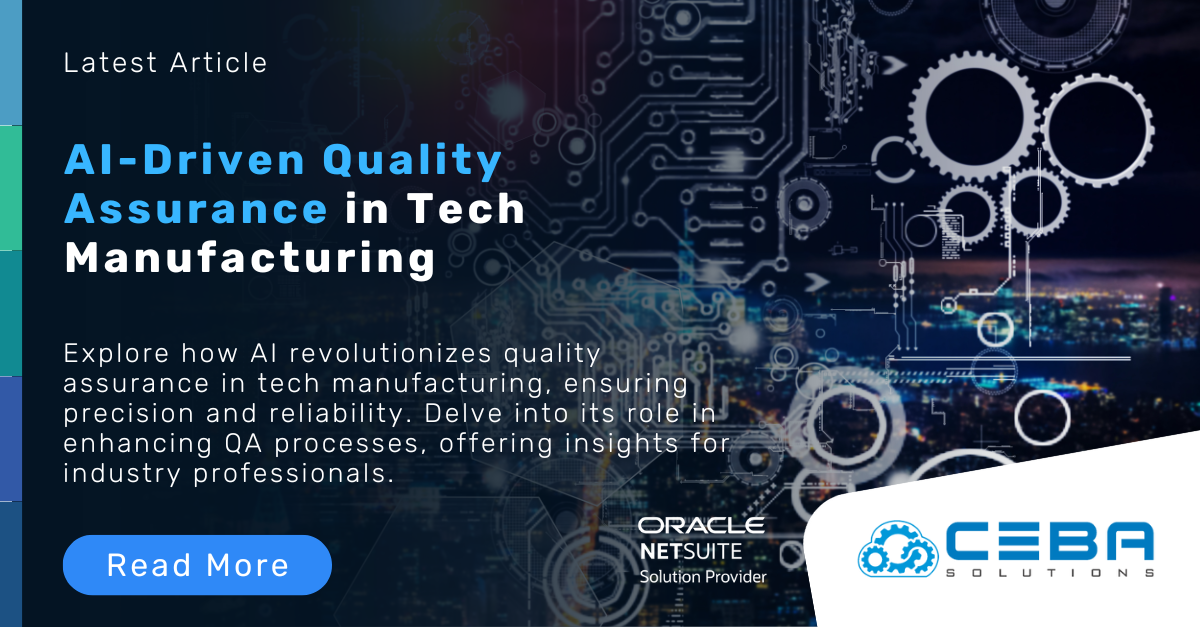
AI-Driven Quality Assurance in Tech Manufacturing
AI-Driven Quality Assurance in Tech Manufacturing
In the highly competitive world of tech manufacturing, maintaining high standards of quality is crucial. As products become more sophisticated and consumer expectations rise, traditional quality assurance (QA) methods are often insufficient to meet the demands of the market. Artificial Intelligence (AI) has emerged as a transformative force in QA, offering advanced solutions that enhance precision, efficiency, and consistency. This article explores how AI-driven quality assurance is revolutionizing tech manufacturing and the benefits it brings to the industry.
The Evolution of Quality Assurance in Tech Manufacturing
Quality assurance in tech manufacturing traditionally involves a combination of manual inspections, statistical sampling, and automated testing. While these methods have been effective to a degree, they often fall short in detecting subtle defects, handling large volumes of data, and adapting to new manufacturing processes.
Human Error: Manual inspections are prone to human error and can be inconsistent. Inspectors might miss subtle defects due to fatigue, oversight, or varying levels of expertise. This inconsistency can lead to significant quality variations in products, which in turn can affect customer satisfaction and brand reputation.
Scalability: As production scales up, manual QA becomes less feasible and more costly. It is difficult to maintain high accuracy and speed with human inspectors alone when dealing with large volumes of products. Automated systems, although helpful, are limited by their static nature and lack of adaptability to new types of defects.
Complexity: Modern tech products are highly complex, requiring more advanced QA methods to ensure all components meet stringent quality standards. Traditional QA methods struggle to keep pace with the intricacies of contemporary manufacturing processes, especially as devices become more miniaturized and multifunctional.
How AI-Driven Quality Assurance Works
AI-driven quality assurance leverages machine learning, computer vision, and big data analytics to enhance the QA process. Here are some key components of AI-driven QA:
Machine Learning Algorithms
Anomaly Detection: Machine learning algorithms are trained on large datasets to detect anomalies and defects in real-time. These algorithms learn from historical data to identify patterns and predict potential quality issues, enabling swift intervention before problems escalate. This predictive capability significantly enhances the precision and reliability of QA processes.
Predictive Analytics: AI uses predictive analytics to forecast potential defects and failures before they occur. This proactive approach helps manufacturers address issues early in the production process, reducing downtime and improving overall efficiency. By anticipating problems before they happen, manufacturers can take preventative measures, thus maintaining continuous production flow and high product quality.
Computer Vision
Automated Visual Inspection: Computer vision systems use cameras and image processing algorithms to inspect products for defects. These systems can identify minute imperfections that are often missed by human inspectors, ensuring a higher standard of quality. Automated visual inspection systems can operate at speeds that far exceed human capabilities, making them ideal for high-volume production environments.
High-Speed Analysis: Computer vision enables high-speed analysis of products, ensuring that even fast-moving production lines maintain stringent quality standards. This capability significantly boosts the efficiency of the QA process. High-speed analysis allows for immediate detection and correction of defects, minimizing the production of faulty products and reducing waste.
Big Data Analytics
Data Integration: AI integrates data from various sources, including sensors, production logs, and quality reports, to provide a comprehensive view of the manufacturing process. This holistic approach helps in identifying the root causes of defects and optimizing processes. By consolidating data from different stages of production, manufacturers can gain deeper insights into their operations and make more informed decisions.
Insight Generation: Big data analytics helps generate actionable insights by identifying trends, correlations, and root causes of quality issues. These insights guide continuous improvement efforts, enhancing product quality over time. Analytics can reveal hidden patterns and relationships in the data that might not be apparent through traditional analysis methods.
Benefits of AI-Driven Quality Assurance
Enhanced Precision and Accuracy
Consistent Inspections: AI systems provide consistent and accurate inspections, reducing the variability associated with human inspections. This ensures a uniform standard of quality across all products. Consistent inspections help build customer trust and loyalty, as consumers receive products that consistently meet or exceed their expectations.
Detection of Subtle Defects: AI can detect subtle defects and anomalies that are difficult to identify with traditional methods, ensuring higher product quality. This capability is critical in maintaining the integrity and performance of high-tech products. By catching defects early, manufacturers can prevent defective products from reaching the market, thereby protecting their brand reputation.
Increased Efficiency and Productivity
Real-Time Monitoring: AI-driven QA systems monitor production in real-time, allowing for immediate detection and correction of defects. This real-time capability minimizes the impact of defects on the production process. Real-time monitoring helps maintain a smooth production flow and reduces the likelihood of costly recalls or rework.
Reduced Downtime: Predictive analytics help prevent equipment failures and production stoppages, reducing downtime and increasing overall productivity. By addressing potential issues before they become critical, AI enhances operational efficiency. Reduced downtime means that production lines can operate continuously, meeting production targets and deadlines more effectively.
Cost Savings
Lower Labor Costs: Automating QA processes reduces the need for manual inspections, lowering labor costs and minimizing the risk of human error. This cost-saving measure allows for the reallocation of human resources to more strategic tasks. Automation helps manufacturers manage labor costs more effectively while maintaining high quality standards.
Reduced Waste: By catching defects early in the production process, AI-driven QA helps reduce waste and rework costs. This not only saves money but also promotes more sustainable manufacturing practices. Reduced waste means that fewer materials and resources are consumed, contributing to more environmentally friendly production processes.
Scalability and Flexibility
Adaptability: AI systems can adapt to different products and production lines, providing flexible QA solutions that scale with manufacturing needs. This adaptability ensures that QA processes can evolve alongside product innovations. Manufacturers can quickly adjust their QA processes to accommodate new products, technologies, and production methods.
Continuous Improvement: Machine learning algorithms continuously learn and improve, enhancing their accuracy and effectiveness over time. This ongoing improvement ensures that QA processes remain cutting-edge and effective. Continuous improvement helps manufacturers stay ahead of quality issues and maintain high standards as their operations grow and evolve.
Improved Customer Satisfaction
Higher Quality Products: Consistent and accurate QA ensures that products meet or exceed customer expectations, leading to higher satisfaction and loyalty. High-quality products build brand reputation and customer trust. Satisfied customers are more likely to become repeat buyers and advocates for the brand.
Fewer Returns and Recalls: Reducing the number of defective products reaching the market minimizes returns and recalls, protecting the brand’s reputation. This not only saves costs but also enhances customer experience and satisfaction. Minimizing returns and recalls helps maintain positive customer relationships and reduces the financial impact of defective products.
Implementation of AI-Driven Quality Assurance
Data Collection and Integration
Comprehensive Data: Collect comprehensive data from all stages of the manufacturing process, including sensor data, production logs, and quality reports. High-quality data is the foundation of effective AI models. Comprehensive data collection ensures that AI systems have a complete and accurate view of the production process.
Data Integration: Integrate data from various sources to create a unified dataset that AI algorithms can analyze. This integrated approach ensures that all relevant information is considered in the QA process. Data integration helps eliminate data silos and provides a holistic view of manufacturing operations.
Training Machine Learning Models
Historical Data: Use historical data to train machine learning models, helping them learn to identify patterns and predict defects. Historical data provides a baseline for AI models to understand normal operating conditions and identify deviations. By learning from past data, AI models can make more accurate predictions about future quality issues.
Continuous Learning: Continuously update and retrain models with new data to improve their accuracy and adaptability. Ongoing learning ensures that AI models remain relevant and effective as production processes evolve. Continuous learning helps AI systems stay current with the latest production trends and challenges.
Implementing Computer Vision Systems
High-Resolution Cameras: Install high-resolution cameras at key points in the production line to capture detailed images of products. High-quality imagery is essential for accurate defect detection. High-resolution cameras provide the clarity and detail needed to identify even the smallest defects.
Image Processing Algorithms: Develop and implement image processing algorithms to analyze visual data and detect defects. These algorithms are the backbone of automated visual inspection systems. Image processing algorithms can quickly and accurately identify defects, ensuring that only high-quality products move forward in the production process.
Integrating Predictive Analytics
Real-Time Monitoring: Implement real-time monitoring systems that use predictive analytics to forecast potential defects and failures. Real-time monitoring allows for immediate corrective actions, minimizing the impact of defects. Predictive analytics helps manufacturers stay ahead of quality issues and maintain continuous production.
Proactive Maintenance: Use predictive insights to schedule proactive maintenance and prevent equipment failures. Proactive maintenance ensures that equipment operates optimally, reducing downtime and maintenance costs. By addressing potential issues before they become critical, manufacturers can maintain high levels of productivity and efficiency.
Employee Training and Support
Training Programs: Develop training programs to help employees understand and effectively use AI-driven QA systems. Training ensures that employees can leverage AI tools to their full potential. Well-trained employees are essential for the successful implementation and operation of AI-driven QA systems.
Ongoing Support: Provide ongoing support and resources to ensure that employees can troubleshoot and optimize AI systems. Continuous support promotes the effective use and improvement of AI-driven QA processes. Ongoing support helps employees stay current with the latest AI technologies and best practices.
Challenges and Considerations
Data Quality and Quantity
High-Quality Data: Ensure that the data used to train AI models is high-quality, accurate, and representative of the production process. Quality data is critical for the effectiveness of AI-driven QA. Ensuring high-quality data helps AI models make accurate and reliable predictions.
Data Volume: Collect sufficient data to train machine learning models effectively, as insufficient data can limit the accuracy of AI predictions. A large volume of diverse data helps AI models learn more accurately. By collecting and analyzing large amounts of data, manufacturers can improve the performance of their AI systems.
Integration with Existing Systems
Compatibility: Ensure that AI-driven QA systems are compatible with existing manufacturing infrastructure and processes. Compatibility is crucial for seamless integration and operation. Ensuring compatibility helps avoid disruptions and ensures that AI systems can be effectively integrated into existing workflows.
Seamless Integration: Work with technology providers to achieve seamless integration of AI solutions into the production workflow. Effective integration maximizes the benefits of AI-driven QA. Seamless integration helps ensure that AI systems can operate smoothly and effectively alongside existing technologies.
Initial Costs and ROI
Upfront Investment: Be prepared for the initial costs associated with implementing AI-driven QA systems, including hardware, software, and training. Initial investment is necessary for long-term benefits. While initial costs can be significant, the long-term benefits of AI-driven QA can justify the investment.
Long-Term ROI: Focus on the long-term return on investment, considering the cost savings, efficiency gains, and quality improvements that AI can deliver. Long-term ROI justifies the initial investment in AI technology. By focusing on long-term benefits, manufacturers can make informed decisions about investing in AI-driven QA.
Conclusion
AI-driven quality assurance is transforming tech manufacturing by providing enhanced precision, efficiency, and scalability. By leveraging machine learning, computer vision, and big data analytics, businesses can improve product quality, reduce costs, and increase customer satisfaction. Implementing AI-driven QA requires careful planning, data integration, and employee training, but the benefits far outweigh the challenges. As AI technology continues to evolve, its impact on quality assurance in tech manufacturing will only grow, driving innovation and excellence in the industry. Embracing AI for quality assurance is not just a competitive advantage but a necessary step toward the future of manufacturing. By adopting AI-driven QA systems, manufacturers can achieve higher levels of quality and efficiency, ensuring their products meet the highest standards and their operations remain competitive in a rapidly evolving market.