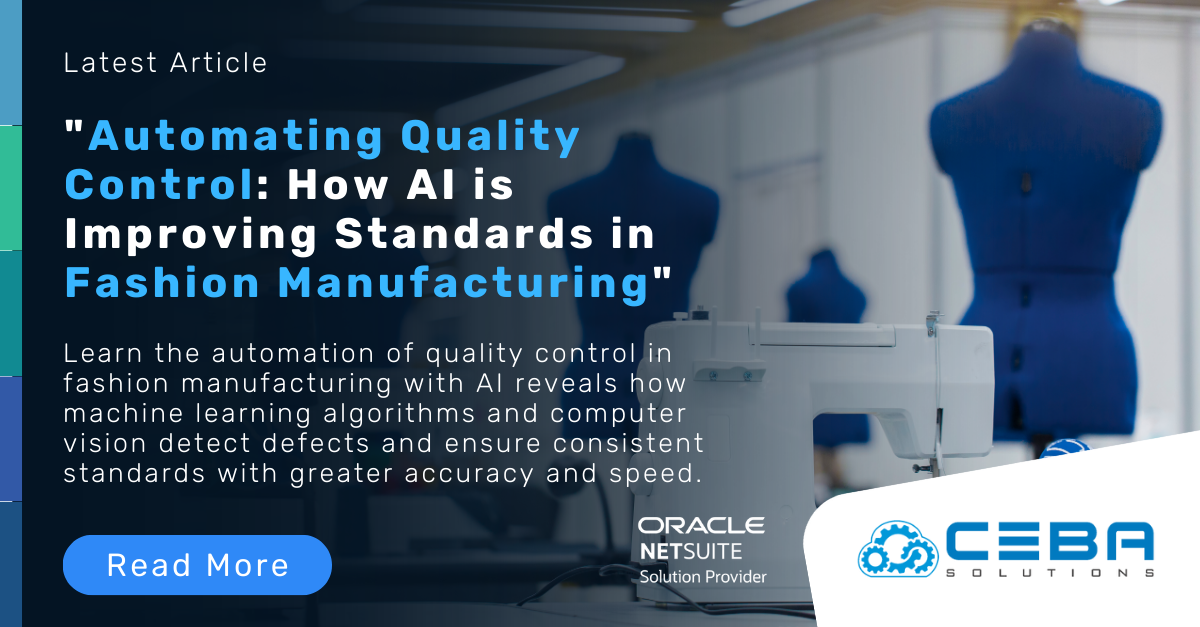
Automating Quality Control: How AI is Improving Standards in Fashion Manufacturing
Automating Quality Control: How AI is Improving Standards in Fashion Manufacturing
In the competitive and detail-oriented world of fashion manufacturing, maintaining high standards of quality is crucial for brand reputation and customer satisfaction. Artificial Intelligence (AI) is revolutionizing the way quality control is conducted in fashion manufacturing by automating inspections and enhancing precision. This article explores the impact of AI on quality control processes, demonstrating how it helps maintain impeccable standards efficiently and consistently.
1. AI-Powered Visual Inspection Systems
Overview of AI-Powered Visual Inspection
AI technologies are being used to implement automated visual inspection systems in fashion manufacturing. These systems use high-resolution cameras and machine learning algorithms to scrutinize garments and fabrics at various stages of the production process. They are trained to detect anomalies, defects, and variations from established quality standards, ensuring that only products meeting all criteria move forward in the production line.
Benefits:
Increased Accuracy: AI systems can identify defects that are often too subtle for the human eye, reducing the likelihood of faulty products reaching the market. This heightened accuracy ensures that only the highest quality items make it to the customers, thereby protecting the brand's reputation and customer satisfaction.
Enhanced Efficiency: Automated inspections are significantly faster than manual checks, speeding up the production process without compromising on quality. This increased efficiency not only boosts production speed but also reduces labor costs associated with manual inspections, providing economic benefits to the manufacturers.
Real-World Application:
For instance, a major fashion brand implemented an AI-powered inspection system in their manufacturing units, resulting in a 30% reduction in defective products and a 20% increase in overall production speed. The system's ability to detect minute flaws that human inspectors often missed played a pivotal role in improving product quality. This implementation not only enhanced the brand’s quality assurance but also increased their operational efficiency, allowing them to meet market demand more effectively.
2. Predictive Maintenance of Manufacturing Equipment
Overview of Predictive Maintenance
AI not only enhances product inspections but also predicts when manufacturing equipment requires maintenance. By analyzing data from machine operations, AI predicts potential failures before they occur, allowing for timely maintenance to prevent machine breakdowns that could compromise product quality.
Benefits:
Reduced Downtime: Keeping equipment in optimal condition minimizes unexpected breakdowns that can cause production delays and quality issues. Predictive maintenance helps in scheduling repairs and maintenance activities during non-peak times, ensuring uninterrupted production flow.
Longer Equipment Lifespan: Regular, data-driven maintenance extends the life of manufacturing equipment, ensuring consistent quality control. By addressing potential issues before they become serious problems, manufacturers can avoid costly emergency repairs and prolong the operational life of their machinery.
Real-World Application:
A textile manufacturer using AI-driven predictive maintenance saw a 40% reduction in unexpected equipment failures. This proactive approach to maintenance helped them maintain a consistent production flow and significantly reduced costs associated with emergency repairs. By implementing AI for predictive maintenance, the manufacturer not only improved operational efficiency but also ensured a stable and reliable production environment, which is crucial for maintaining high-quality standards.
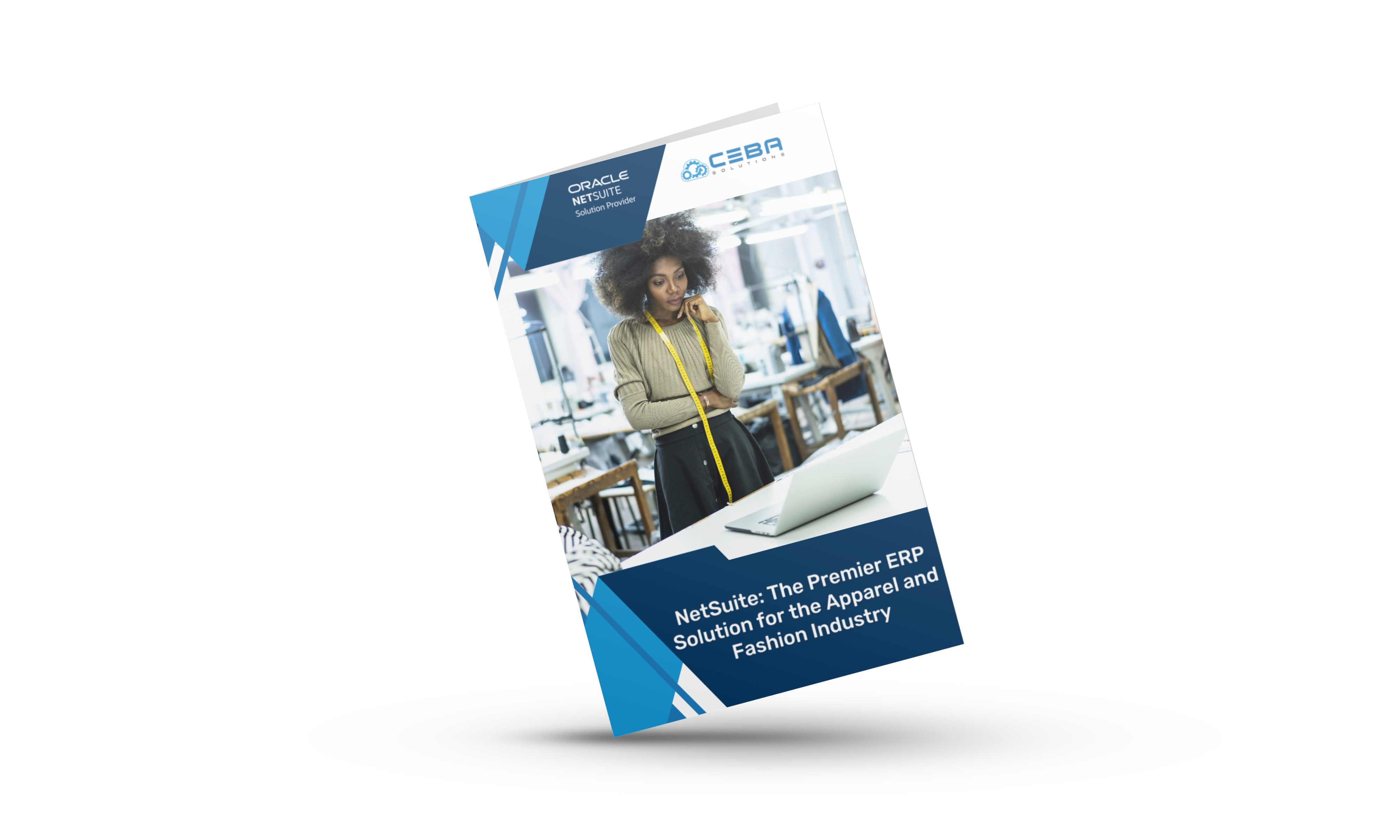
3. Integration with Manufacturing Execution Systems (MES)
Overview of AI and MES Integration
AI integrates seamlessly with Manufacturing Execution Systems (MES), providing a holistic view of the production process. This integration enables real-time tracking of quality data across different stages and batches of production, allowing for immediate adjustments to maintain quality standards.
Benefits:
Real-Time Quality Monitoring: AI provides immediate insights into quality metrics, helping manufacturers quickly address any deviations from quality standards. This real-time monitoring allows for swift corrective actions, ensuring that quality issues are identified and resolved promptly, thereby minimizing the production of defective items.
Consistency Across Batches: By monitoring and adjusting production parameters in real-time, AI ensures that every batch of products meets uniform quality standards. This consistency enhances brand reliability and customer trust, as consumers can be confident that every item they purchase meets the same high-quality criteria.
Real-World Application:
By integrating AI with MES, a clothing manufacturer was able to monitor and adjust production parameters in real-time, resulting in a 25% improvement in quality consistency across all product lines. This integration helped them swiftly identify and rectify quality issues, ensuring that all products met their rigorous standards. The ability to maintain consistent quality across large-scale production runs not only improved the brand’s reputation but also reduced the cost of returns and replacements.
4. Automated Reporting and Compliance Tracking
Overview of Automated Reporting
AI automates the generation of quality reports and compliance documentation, ensuring that all products meet industry standards and regulations. This not only streamlines the audit process but also helps fashion brands maintain transparency with consumers and regulators.
Benefits:
Streamlined Compliance: Automated systems ensure that all necessary quality checks and compliance measures are documented, simplifying legal and regulatory processes. This reduces the administrative burden on quality control teams and ensures that all compliance requirements are consistently met.
Enhanced Traceability: AI provides detailed records of quality controls for every product, increasing accountability and traceability. This level of documentation is invaluable during audits and helps brands demonstrate their commitment to quality and regulatory compliance.
Real-World Application:
A global fashion retailer utilized AI to automate compliance reporting, reducing the time spent on regulatory documentation by 50%. This automation ensured that all products adhered to international standards, enhancing their credibility and customer trust. The ability to quickly generate accurate compliance reports also allowed the retailer to respond more effectively to regulatory inquiries and audits.
5. Data-Driven Quality Improvement
Overview of Data-Driven Improvement
By collecting and analyzing data from every quality inspection, AI helps identify patterns and trends related to defects and quality issues. This information is invaluable for continuous improvement efforts, allowing manufacturers to refine their processes and prevent recurring issues.
Benefits:
Continuous Improvement: Ongoing data analysis helps manufacturers enhance production processes and product quality over time. By understanding the root causes of defects, manufacturers can implement targeted improvements that lead to higher quality products and more efficient operations.
Reduced Waste and Cost: Identifying and addressing recurring quality issues reduces waste and associated costs, improving overall operational efficiency. This not only benefits the manufacturer financially but also supports sustainability efforts by minimizing material waste.
Real-World Application:
A leading apparel manufacturer used AI analytics to track and analyze defect patterns, leading to a 15% reduction in waste and significant cost savings. The insights gained from data analysis allowed them to implement targeted improvements in their production process, reducing defect rates and boosting overall efficiency. This data-driven approach to quality control ensured that the manufacturer could maintain high standards while continuously improving their processes.
Conclusion
AI is setting new standards in fashion manufacturing quality control, providing tools that enhance accuracy, efficiency, and consistency. By automating inspections and integrating data-driven processes, AI not only upholds high-quality standards but also drives continual improvement in manufacturing practices. As AI technologies evolve, their role in ensuring product excellence and brand integrity in fashion manufacturing will become increasingly indispensable.
Incorporating AI into quality control processes not only benefits manufacturers by improving efficiency and reducing costs but also ensures that consumers receive high-quality products. The future of fashion manufacturing looks promising with AI paving the way for smarter, more reliable, and sustainable practices. By leveraging AI, fashion manufacturers can achieve unprecedented levels of quality control, ensuring that every product meets the highest standards and enhances brand reputation in a competitive market.