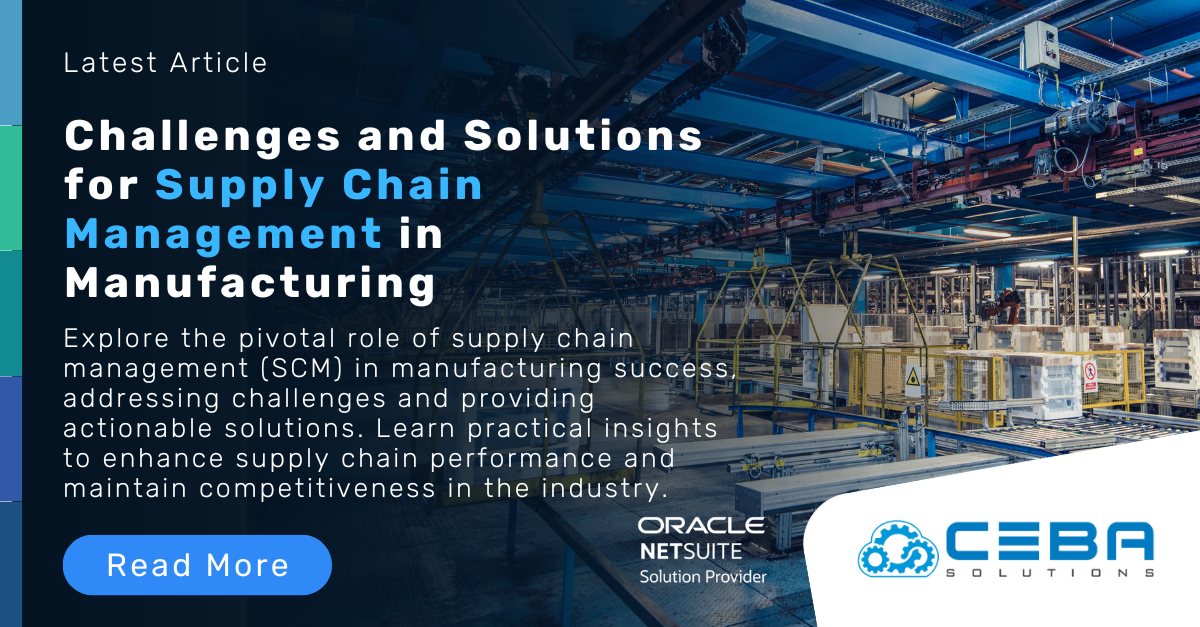
Challenges and Solutions for Supply Chain Management in Manufacturing
Challenges and Solutions for Supply Chain Management in Manufacturing
Supply chain management (SCM) is the backbone of manufacturing operations, ensuring the seamless flow of materials, information, and finances from suppliers to customers. Efficient supply chain management is crucial for maintaining production schedules, minimizing costs, and meeting customer demands. However, manufacturers face numerous challenges in managing their supply chains, ranging from disruptions and complexity to changing market dynamics. This article explores the key challenges in supply chain management for manufacturing and provides practical solutions to address these issues.
Challenges in Supply Chain Management
- Supply Chain Disruptions:
- Natural Disasters: Events such as earthquakes, floods, and hurricanes can disrupt the supply chain by damaging infrastructure and halting transportation.
- Pandemics: The COVID-19 pandemic highlighted vulnerabilities in global supply chains, causing widespread disruptions due to lockdowns, labor shortages, and transport restrictions.
- Political Instability: Trade wars, tariffs, and political unrest can create uncertainties and delays in the supply chain.
- Complexity and Globalization:
- Global Sourcing: Sourcing materials and components from multiple countries increases the complexity of managing the supply chain, including dealing with different regulations, customs procedures, and cultural differences.
- Extended Supply Chains: Longer supply chains with multiple tiers of suppliers and intermediaries can make visibility and coordination more challenging.
- Demand Variability:
- Fluctuating Customer Demand: Rapid changes in customer preferences and market conditions can lead to demand variability, making it difficult to forecast and plan inventory levels accurately.
- Seasonal Demand: Some industries experience significant seasonal fluctuations in demand, requiring flexible and responsive supply chain strategies.
- Inventory Management:
- Overstocking: Excess inventory ties up capital and incurs storage costs, while also risking obsolescence and spoilage.
- Stockouts: Insufficient inventory can lead to production delays, lost sales, and dissatisfied customers.
- Supplier Reliability:
- Supplier Performance: Inconsistent quality, late deliveries, and financial instability of suppliers can disrupt manufacturing operations.
- Single Sourcing Risks: Relying on a single supplier for critical components can be risky if the supplier faces disruptions.
- Technological Integration:
- Legacy Systems: Many manufacturers still use outdated legacy systems that lack integration capabilities, leading to inefficiencies and data silos.
- Cybersecurity Risks: Increasing digitalization of supply chains introduces cybersecurity threats that can compromise sensitive information and disrupt operations.
Solutions for Effective Supply Chain Management
- Risk Management and Resilience:
- Diversification: Diversify suppliers and sourcing locations to reduce dependency on a single source and mitigate risks associated with regional disruptions.
- Risk Assessment: Conduct regular risk assessments to identify potential vulnerabilities and develop contingency plans for different scenarios.
- Inventory Buffers: Maintain strategic inventory buffers for critical components to cushion against supply chain disruptions.
- Enhanced Visibility and Transparency:
- Supply Chain Mapping: Create detailed maps of the entire supply chain, including all suppliers, intermediaries, and logistics providers, to improve visibility and coordination.
- Real-Time Tracking: Implement IoT devices and GPS tracking systems to monitor the movement of goods in real-time, ensuring timely deliveries and reducing uncertainties.
- Blockchain Technology: Utilize blockchain for secure and transparent tracking of transactions and product provenance, enhancing trust and accountability.
- Demand Forecasting and Planning:
- Advanced Analytics: Use advanced analytics and machine learning algorithms to improve demand forecasting accuracy and predict market trends.
- Collaborative Planning: Collaborate with suppliers and customers to share demand forecasts and production plans, ensuring alignment and reducing variability.
- Agile Practices: Adopt agile supply chain practices that allow for quick adjustments in response to changing demand and market conditions.
- Inventory Optimization:
- Just-In-Time (JIT): Implement JIT inventory practices to reduce excess inventory and minimize waste, while ensuring that materials are available when needed.
- Safety Stock Levels: Determine optimal safety stock levels based on demand variability, lead times, and service level requirements to balance inventory costs and availability.
- Automated Replenishment: Use automated inventory management systems to monitor stock levels and trigger replenishment orders based on predefined thresholds.
- Supplier Relationship Management:
- Supplier Evaluation: Regularly evaluate supplier performance based on quality, delivery reliability, and financial stability to ensure alignment with organizational goals.
- Strategic Partnerships: Develop long-term strategic partnerships with key suppliers, fostering collaboration, innovation, and mutual growth.
- Multi-Sourcing: Establish relationships with multiple suppliers for critical components to reduce dependency and increase flexibility.
- Technological Integration:
- ERP Systems: Implement integrated Enterprise Resource Planning (ERP) systems to centralize data, streamline processes, and improve information flow across the supply chain.
- Cloud-Based Solutions: Adopt cloud-based supply chain management solutions for scalable, flexible, and accessible data management and collaboration.
- Cybersecurity Measures: Invest in robust cybersecurity measures, including encryption, firewalls, and regular security audits, to protect sensitive supply chain data.
Conclusion
Effective supply chain management is crucial for manufacturing success, especially in the face of increasing complexity and uncertainty. By addressing challenges such as disruptions, demand variability, and supplier reliability, manufacturers can build resilient and efficient supply chains. Implementing solutions such as enhanced visibility, advanced analytics, and technological integration can drive significant improvements in productivity, cost efficiency, and customer satisfaction. As the manufacturing landscape continues to evolve, embracing innovative supply chain strategies will be key to maintaining a competitive edge and achieving long-term growth.