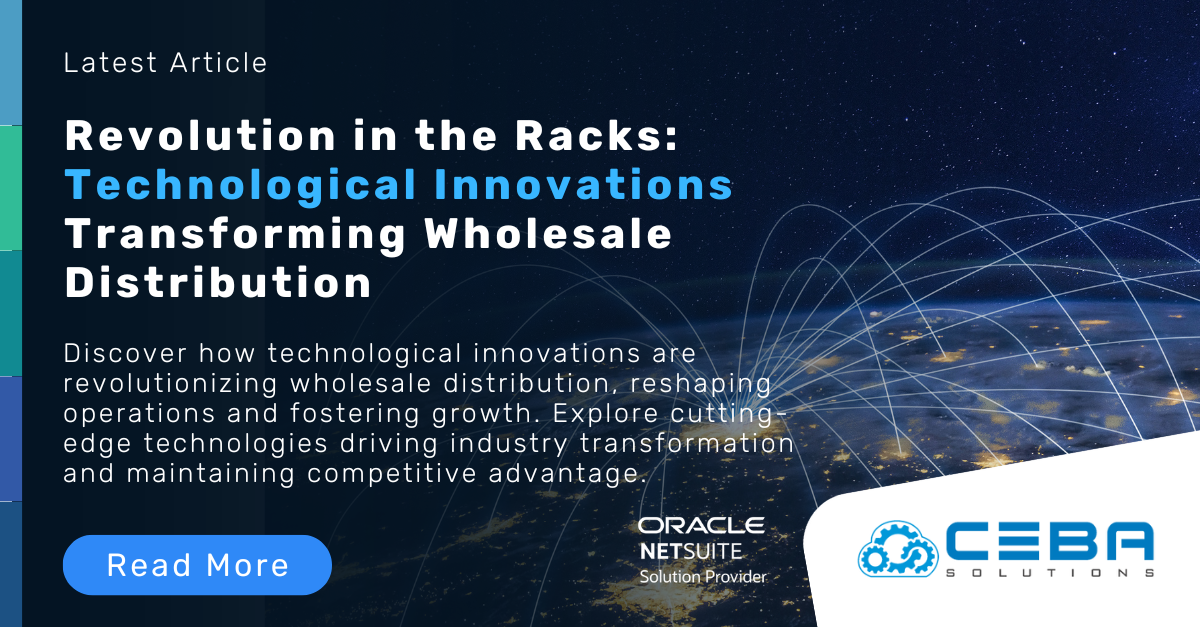
Revolution in the Racks: Technological Innovations Transforming Wholesale Distribution
Revolution in the Racks: Technological Innovations Transforming Wholesale Distribution
The wholesale distribution industry is undergoing a profound transformation driven by technological innovations. As digital technologies advance and customer expectations evolve, wholesalers are adopting new tools and systems to enhance efficiency, improve accuracy, and stay competitive. From automation and artificial intelligence to blockchain and the Internet of Things (IoT), these innovations are revolutionizing how goods are stored, managed, and delivered. This article explores the key technological innovations transforming wholesale distribution and their impact on the industry.
The Role of Technology in Wholesale Distribution
Efficiency and Accuracy: Technology enhances operational efficiency and accuracy by automating processes, reducing manual errors, and optimizing workflows. Automation tools, such as robotic process automation (RPA) and warehouse management systems (WMS), streamline tasks like order picking, packing, and inventory tracking. This not only speeds up operations but also minimizes human error, ensuring that products are correctly handled and dispatched. For example, barcode scanners and RFID (Radio Frequency Identification) systems can track inventory in real-time, providing precise data on stock levels and movement.
Cost Reduction: Technological innovations help reduce operational costs by streamlining processes, improving inventory management, and optimizing resource utilization. Advanced analytics and machine learning algorithms can predict demand more accurately, helping wholesalers maintain optimal inventory levels and reduce holding costs. Additionally, energy-efficient technologies and automated systems reduce labor and energy expenses, contributing to overall cost savings. For instance, automated guided vehicles (AGVs) can transport goods within warehouses more efficiently than manual labor, cutting down on time and labor costs.
Customer Satisfaction: Advanced technologies enable faster and more reliable deliveries, enhancing customer satisfaction and loyalty. Technologies like IoT and GPS tracking provide real-time updates on shipment status, allowing customers to track their orders accurately and receive timely notifications. Furthermore, artificial intelligence (AI) can optimize delivery routes, ensuring quicker and more efficient deliveries. The use of drones for last-mile delivery is an emerging trend that promises even faster delivery times, particularly in urban areas.
Competitive Advantage: Early adoption of cutting-edge technologies provides a competitive edge by improving service quality and operational capabilities. Companies that leverage advanced technologies can offer superior services, such as same-day delivery, personalized customer experiences, and proactive issue resolution. This technological edge not only attracts new customers but also retains existing ones by consistently meeting or exceeding their expectations. Additionally, technologies like blockchain enhance transparency and traceability in the supply chain, building trust and credibility with customers and partners.
Key Technological Innovations in Wholesale Distribution
Automation and Robotics: Automation and robotics are at the forefront of the transformation in wholesale distribution. Automated storage and retrieval systems (AS/RS) and robotics enhance warehouse efficiency by automating repetitive tasks and enabling round-the-clock operations. These systems improve accuracy in inventory management and speed up the order fulfillment process. Robotics can also assist in sorting and packaging, reducing the time and effort required for these tasks and allowing human workers to focus on more complex activities.
Artificial Intelligence and Machine Learning: AI and machine learning algorithms are revolutionizing demand forecasting, inventory management, and customer service. Predictive analytics enable wholesalers to anticipate demand fluctuations and adjust inventory levels accordingly, reducing stockouts and overstock situations. AI-powered chatbots and virtual assistants enhance customer service by providing instant responses to inquiries and assisting with order processing. Machine learning can also identify patterns and trends in customer behavior, enabling more personalized and targeted marketing strategies.
Blockchain Technology: Blockchain technology offers unparalleled transparency and security in supply chain management. By creating an immutable ledger of transactions, blockchain ensures that every step in the supply chain is recorded and verifiable. This enhances traceability, making it easier to track the origin and movement of products, which is crucial for quality assurance and regulatory compliance. Blockchain can also streamline payment processes by reducing the need for intermediaries, thus speeding up transactions and reducing costs.
Internet of Things (IoT): IoT devices and sensors provide real-time data on various aspects of the supply chain, from inventory levels to equipment health. These sensors can monitor temperature, humidity, and other environmental factors to ensure that products, especially perishable goods, are stored and transported under optimal conditions. IoT-enabled devices can also track the location of shipments in real time, providing valuable insights into the supply chain's efficiency and identifying potential bottlenecks or delays.
Cloud Computing: Cloud computing offers scalable and flexible solutions for data storage, processing, and management. Cloud-based platforms enable wholesalers to access real-time data from anywhere, facilitating better decision-making and collaboration across different locations. These platforms also support advanced analytics and integration with other digital tools, enhancing overall operational efficiency. By leveraging cloud computing, wholesalers can quickly adapt to changing market demands and scale their operations without significant upfront investments in IT infrastructure.
Impact of Technological Innovations on Wholesale Distribution
Enhanced Operational Efficiency
Process Optimization: Automation and AI optimize warehouse operations, from receiving and storing goods to picking and shipping orders. This reduces cycle times and increases throughput. For example, automated guided vehicles (AGVs) can move goods within the warehouse more efficiently than human workers, while AI-driven systems can dynamically allocate tasks to the most appropriate resources based on real-time data, minimizing downtime and bottlenecks.
Resource Utilization: Technologies such as IoT and AI optimize the use of resources, including labor, equipment, and space, leading to cost savings and higher productivity. IoT sensors can monitor the condition and utilization of equipment, ensuring maintenance is performed proactively, reducing downtime. AI algorithms can analyze data to optimize warehouse layouts and workflows, making the best use of available space and ensuring that labor is allocated effectively.
Improved Inventory Management
Accurate Forecasting: AI-driven demand forecasting improves the accuracy of inventory planning, reducing the risk of overstocking or stockouts. Machine learning models analyze historical data and market trends to predict future demand with greater precision, enabling wholesalers to maintain optimal inventory levels. This not only reduces holding costs but also ensures that products are available when customers need them.
Real-Time Visibility: IoT-enabled tracking provides real-time visibility into inventory levels and movements, enabling better inventory control and faster response to changes in demand. For instance, RFID tags and IoT sensors can track items throughout the warehouse and supply chain, providing up-to-the-minute data on their location and status. This visibility allows for more responsive and flexible inventory management, reducing the likelihood of disruptions.
Increased Customer Satisfaction
Faster Deliveries: Automation and real-time tracking enable faster order fulfillment and delivery, meeting customer expectations for quick and reliable service. Automated picking systems and optimized delivery routes, guided by AI, ensure that orders are processed and shipped efficiently. Real-time tracking allows customers to monitor their deliveries, providing assurance and enhancing the overall service experience.
Better Communication: Advanced inventory and order management systems provide timely updates to customers regarding order status, enhancing transparency and trust. Automated notifications and real-time tracking information keep customers informed at every stage of their order's journey, from processing to delivery. This improved communication builds trust and can lead to higher customer satisfaction and loyalty.
Enhanced Supply Chain Transparency
Traceability: Blockchain technology ensures traceability of products throughout the supply chain, helping to verify the authenticity and origin of goods and reducing the risk of fraud. Every transaction and movement of goods is recorded on a blockchain ledger, creating an immutable and transparent record that can be audited at any time. This traceability is especially important for industries where product authenticity and safety are critical, such as pharmaceuticals and food.
Compliance: Enhanced transparency and smart contracts ensure compliance with regulatory requirements and contractual agreements, reducing the risk of disputes. Smart contracts automatically enforce the terms of agreements and ensure that all parties meet their obligations, while blockchain provides a verifiable record of compliance activities. This reduces the administrative burden and helps avoid legal and regulatory issues.
Reduced Operational Costs
Labor Savings: Automation reduces the need for manual labor, lowering labor costs and minimizing the risk of human error. Automated systems handle repetitive and labor-intensive tasks, allowing human workers to focus on more complex and strategic activities. This not only cuts costs but also enhances accuracy and efficiency.
Energy Efficiency: IoT-enabled environmental monitoring optimizes energy usage in warehouses, reducing utility costs and supporting sustainability initiatives. Sensors can adjust lighting, heating, and cooling based on real-time occupancy and environmental conditions, ensuring that energy is used efficiently. This not only lowers operating costs but also reduces the environmental footprint of warehouse operations.
Strategies for Implementing Technological Innovations
Assess Business Needs
Identify Pain Points: Assess your current operations to identify pain points and areas for improvement. Conduct a thorough analysis of your processes to pinpoint inefficiencies, bottlenecks, and areas where manual efforts lead to errors or delays. Engage with employees and stakeholders to gather insights on daily challenges they face. This comprehensive understanding will help determine which technologies can address these challenges and add value to your business. For example, if order processing is slow and error-prone, automation tools could streamline this process.
Set Clear Goals: Define clear goals and objectives for implementing new technologies, such as improving efficiency, reducing costs, or enhancing customer satisfaction. These goals should be specific, measurable, achievable, relevant, and time-bound (SMART). Clear objectives provide direction and enable you to measure the success of your technology implementation. For instance, setting a goal to reduce order fulfillment time by 30% within the next year provides a tangible target to aim for.
Choose the Right Technologies
Evaluate Options: Research and evaluate different technologies to find the best fit for your business needs. Consider factors such as scalability, compatibility with existing systems, and ease of implementation. Assess the potential return on investment (ROI) and how each technology aligns with your long-term strategic goals. Review case studies, seek expert opinions, and compare different solutions to make an informed decision. For instance, if you need a warehouse management system (WMS), compare various WMS providers on features, scalability, and user-friendliness.
Pilot Testing: Conduct pilot tests to evaluate the performance of new technologies in a controlled environment. Select a specific area or process for the pilot test and monitor its impact closely. Gather feedback from users and stakeholders to identify any issues or areas for improvement. This approach allows you to make necessary adjustments and ensures that the technology meets your needs before full-scale implementation. For example, pilot testing a new inventory management system in one warehouse location can reveal potential integration challenges and user training needs.
Invest in Training and Development
Employee Training: Provide training for employees to ensure they understand how to use new technologies effectively. Develop comprehensive training programs that cover both technical skills and the benefits of the technology for their roles. Use a mix of training methods, such as workshops, hands-on sessions, and online tutorials, to accommodate different learning styles. Ensuring that employees are comfortable and proficient with new tools is crucial for successful adoption and maximizing the benefits of the technology.
Continuous Learning: Foster a culture of continuous learning and development, encouraging employees to stay updated with the latest technological advancements and best practices. Promote ongoing education through regular training sessions, access to online courses, and participation in industry conferences and workshops. Keeping employees informed about new technologies and trends helps them adapt quickly and keeps your business at the forefront of innovation.
Collaborate with Technology Partners
Strategic Partnerships: Partner with technology providers, consultants, and industry experts to leverage their expertise and support during the implementation process. These partners can offer valuable insights, best practices, and technical assistance to ensure a smooth transition. Building strong relationships with technology partners can also provide access to the latest innovations and updates in the industry.
Integration Support: Work with technology partners to ensure seamless integration of new systems with existing infrastructure and processes. Effective integration minimizes disruptions and ensures that new technologies complement your current operations. Collaborate closely with your technology providers to develop an integration plan that addresses potential challenges and ensures data consistency across systems.
Monitor and Optimize
Performance Metrics: Monitor key performance metrics to assess the impact of new technologies on your operations. Metrics may include order fulfillment times, inventory accuracy, labor efficiency, and customer satisfaction. Establish a baseline before implementation and regularly track these metrics to measure progress. Analyzing this data helps identify areas where the technology is delivering benefits and where further improvements are needed.
Continuous Improvement: Use data and feedback to continuously refine and optimize your technology implementation. Stay flexible and open to adopting new innovations as they emerge. Encourage a culture of feedback and continuous improvement, where employees are encouraged to share their experiences and suggest enhancements. Regularly review performance metrics and make data-driven decisions to fine-tune processes and ensure that the technology continues to meet your evolving business needs.
Challenges to Consider
Initial Investment
Cost Considerations: Implementing new technologies often requires significant upfront investment. This includes costs for purchasing hardware, software, and possibly new infrastructure. Additionally, there may be hidden costs such as integration with existing systems and potential downtime during the transition. It's crucial to evaluate the long-term benefits and return on investment (ROI) to justify these costs. Conducting a cost-benefit analysis can help determine whether the initial expenditure will lead to sufficient gains in efficiency, productivity, and customer satisfaction over time.
Budget Planning: Plan your budget carefully to allocate resources for technology adoption, including hardware, software, training, and maintenance. This involves not only the initial purchase costs but also ongoing expenses such as subscription fees for software, costs for regular updates, and maintenance contracts. Include a contingency fund to cover unexpected expenses that may arise during the implementation phase. Detailed budgeting ensures that the project stays within financial limits and helps avoid financial strain on other business operations.
Change Management
Employee Resistance: Employees may resist changes due to fear of job displacement or unfamiliarity with new technologies. This resistance can slow down the adoption process and reduce the effectiveness of the new technology. Address concerns through transparent communication and involving them in the change process. Explain the benefits of the technology, provide reassurances about job security, and offer training to help them adapt to new systems. Engaging employees early in the process and seeking their input can also foster a sense of ownership and reduce resistance.
Cultural Shift: Foster a culture that embraces innovation and change. Encourage a growth mindset and highlight the benefits of new technologies for both the business and employees. This can be achieved by recognizing and rewarding adaptability and continuous learning within the organization. Leadership should model positive attitudes towards change and innovation, demonstrating a commitment to staying ahead of technological advancements. Building a culture that values innovation helps ensure that employees are more receptive to new technologies and processes.
Data Security
Cybersecurity Risks: Implement robust cybersecurity measures to protect sensitive data and systems from cyber threats. This includes encryption, secure access controls, and regular security audits. Given the increasing sophistication of cyber-attacks, it's essential to have a comprehensive cybersecurity strategy that includes firewalls, intrusion detection systems, and regular vulnerability assessments. Training employees on cybersecurity best practices is also critical to prevent breaches caused by human error.
Compliance: Ensure compliance with data protection regulations and industry standards to safeguard customer and business data. This involves staying updated with relevant laws such as the General Data Protection Regulation (GDPR) and industry-specific regulations. Regularly review and update your data protection policies and procedures to ensure they meet the latest standards. Non-compliance can result in significant fines and damage to your business's reputation, so it’s crucial to prioritize data security and regulatory adherence.
Conclusion
Technological innovations are revolutionizing wholesale distribution, offering significant benefits in terms of efficiency, accuracy, customer satisfaction, and cost reduction. By embracing automation, AI, IoT, blockchain, and other advanced technologies, wholesalers can transform their operations and stay competitive in a rapidly evolving market. Implementing these innovations requires careful planning, investment in training, collaboration with technology partners, and a commitment to continuous improvement. While there are challenges to consider, the long-term advantages far outweigh the initial hurdles. As technology continues to advance, wholesalers that stay ahead of the curve will be well-positioned to thrive in the future of wholesale distribution.