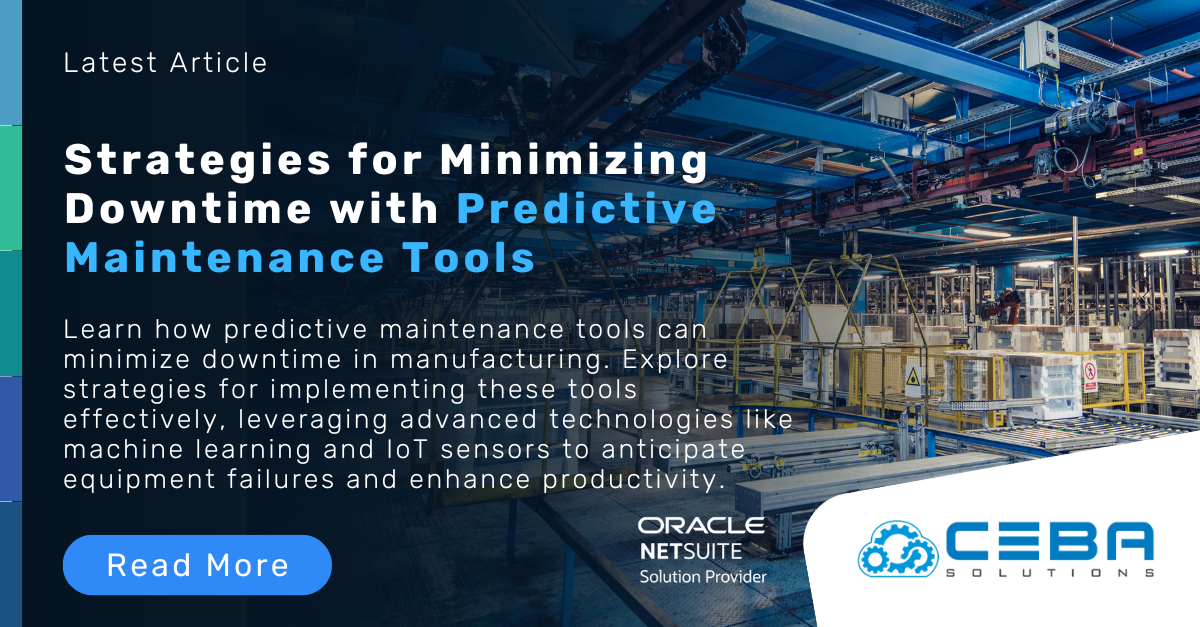
Strategies for Minimizing Downtime with Predictive Maintenance Tools
Strategies for Minimizing Downtime with Predictive Maintenance Tools
In the fast-paced world of industrial operations, minimizing downtime is crucial for maintaining productivity, reducing costs, and ensuring the smooth operation of machinery and equipment. Unplanned downtime can lead to significant financial losses, disrupted schedules, and reduced operational efficiency. Predictive maintenance tools have emerged as a powerful solution to these challenges, offering the ability to foresee and address potential equipment failures before they occur. This article explores the strategies for minimizing downtime using predictive maintenance tools, highlighting the benefits, techniques, and best practices for implementation.
Understanding Predictive Maintenance
Predictive maintenance (PdM) is a proactive maintenance strategy that uses data analysis and monitoring technologies to predict equipment failures and schedule maintenance activities accordingly. Unlike reactive maintenance, which addresses issues after they occur, or preventive maintenance, which follows a predetermined schedule, predictive maintenance aims to optimize maintenance timing based on the actual condition of the equipment.
Benefits of Predictive Maintenance
The adoption of predictive maintenance tools offers several benefits, including:
- Reduced Downtime: By predicting and addressing potential failures before they lead to equipment breakdowns, PdM minimizes unplanned downtime and keeps operations running smoothly.
- Cost Savings: Predictive maintenance reduces the need for emergency repairs and extends the lifespan of equipment, resulting in significant cost savings. It also optimizes the use of maintenance resources and inventory management.
- Improved Safety: By ensuring that equipment is in optimal working condition, predictive maintenance enhances workplace safety and reduces the risk of accidents and injuries.
- Increased Efficiency: PdM helps maintain optimal equipment performance, leading to improved operational efficiency and productivity.
Strategies for Implementing Predictive Maintenance Tools
To effectively minimize downtime with predictive maintenance tools, organizations should adopt the following strategies:
- Data Collection and Monitoring
The foundation of predictive maintenance is accurate and comprehensive data collection. Sensors and IoT (Internet of Things) devices are installed on machinery to continuously monitor various parameters, such as temperature, vibration, pressure, and humidity. This real-time data is collected and transmitted to a centralized system for analysis.
- Advanced Data Analytics
Predictive maintenance relies on advanced data analytics and machine learning algorithms to process and analyze the collected data. These tools identify patterns and trends that indicate potential equipment failures. By leveraging historical data and machine learning models, predictive maintenance systems can provide accurate predictions and insights.
- Condition-Based Monitoring
Condition-based monitoring (CBM) is a key component of predictive maintenance. It involves continuously monitoring the condition of equipment and comparing real-time data to predefined thresholds. When a parameter exceeds its threshold, an alert is generated, prompting maintenance actions before a failure occurs.
- Integration with Maintenance Management Systems
Integrating predictive maintenance tools with existing maintenance management systems (MMS) enhances their effectiveness. This integration allows for seamless scheduling of maintenance tasks, tracking of equipment history, and efficient allocation of resources. It also ensures that maintenance activities are aligned with production schedules, minimizing disruptions.
- Remote Monitoring and Diagnostics
Remote monitoring and diagnostics enable maintenance teams to oversee equipment performance from any location. This capability is particularly valuable for organizations with multiple facilities or remote operations. Remote monitoring allows for timely intervention and reduces the need for on-site inspections, saving time and resources.
- Automated Alerts and Notifications
Automated alerts and notifications are essential for timely maintenance actions. Predictive maintenance systems can be configured to send alerts via email, SMS, or mobile apps when potential issues are detected. These alerts provide detailed information about the equipment's condition and recommended actions, enabling maintenance teams to respond quickly and effectively.
- Predictive Maintenance Scheduling
Predictive maintenance scheduling involves planning maintenance activities based on the predicted remaining useful life (RUL) of equipment components. By scheduling maintenance tasks at the most opportune times, organizations can avoid unnecessary downtime and optimize maintenance resources. Predictive scheduling also helps in coordinating maintenance with production cycles, reducing disruptions.
- Continuous Improvement and Adaptation
Predictive maintenance is an ongoing process that requires continuous improvement and adaptation. Organizations should regularly review and refine their predictive maintenance strategies based on feedback and performance data. This iterative approach ensures that predictive maintenance tools remain effective and aligned with evolving operational needs.
Best Practices for Successful Implementation
To successfully implement predictive maintenance tools and minimize downtime, organizations should follow these best practices:
- Start with Critical Equipment: Focus on implementing predictive maintenance for critical equipment that has the greatest impact on operations. This approach ensures maximum return on investment and minimizes the risk of major disruptions.
- Invest in Training and Education: Equip maintenance teams with the necessary skills and knowledge to use predictive maintenance tools effectively. Ongoing training and education are essential for staying up-to-date with the latest technologies and best practices.
- Leverage Cross-Functional Collaboration: Predictive maintenance requires collaboration between maintenance, operations, and IT teams. Encourage cross-functional communication and collaboration to ensure the successful implementation and integration of predictive maintenance tools.
- Measure and Analyze Results: Continuously measure and analyze the results of predictive maintenance efforts. Key performance indicators (KPIs) such as downtime reduction, cost savings, and maintenance efficiency should be tracked to assess the effectiveness of predictive maintenance strategies.
- Scale and Expand Gradually: Start with a pilot program and gradually scale predictive maintenance across the organization. This phased approach allows for the identification and resolution of challenges before full-scale implementation.
Conclusion
Predictive maintenance tools are revolutionizing the way organizations manage their equipment and minimize downtime. By leveraging data analytics, condition-based monitoring, and advanced technologies, predictive maintenance enables proactive maintenance actions that enhance operational efficiency, reduce costs, and improve safety. Implementing these strategies requires careful planning, collaboration, and continuous improvement, but the benefits of predictive maintenance make it a worthwhile investment for organizations seeking to optimize their operations and achieve long-term sustainability.