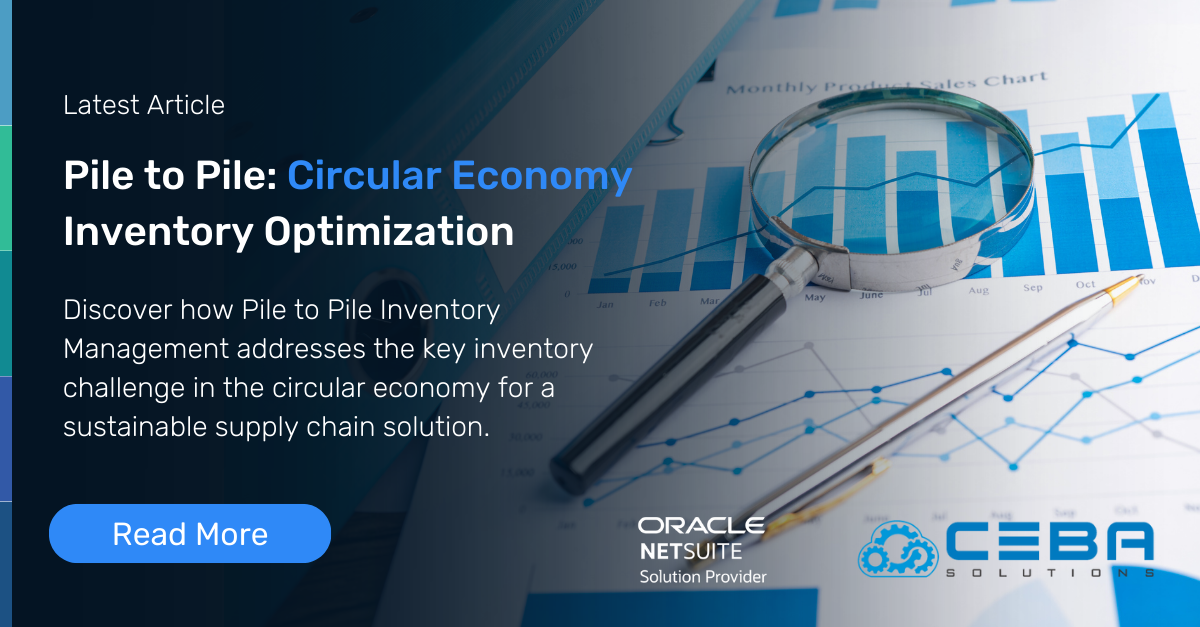
Pile to Pile Inventory Management - The Key Inventory Challenge for the Circular Economy
Pile to Pile Inventory Management - The Key Inventory Challenge for the Circular Economy
In the quest for sustainability, businesses across many industries are shifting towards models that support the circular economy - an economic model that prioritizes the reuse, recycling, and remanufacturing of materials to minimize waste.
This article delves into pile to pile inventory management, the software challenges associated with managing it and its role in the circular economy, and why it presents unique inventory challenges. You will learn about the strategies for optimizing inventory in this context, the importance of reverse logistics, and how businesses can tackle these hurdles to achieve a sustainable and efficient supply chain.
Understanding Pile to Pile Inventory Management
What is Pile to Pile Inventory Management?
Pile to pile inventory management refers to the system of handling goods that move in cyclical processes, aligning with the principles of the circular economy. Rather than following the traditional linear flow where products are manufactured, sold and discarded; pile to pile inventory management involves the continuous movement of materials back into production after they have reached the end of their initial lifecycle. This can include reused, remanufactured, or recycled materials being put back into the supply chain, creating a closed-loop system.
In essence, this system manages the flow of materials from "pile to pile" - where the pile represents stockpiled materials at different stages, whether raw materials, waste products ready for recycling, or components awaiting refurbishment. The main goal is to keep products, components, and materials in use for as long as possible, extracting maximum value before moving them back into the production cycle.
The Role of Pile to Pile in the Circular Economy
The circular economy seeks to eliminate waste through thoughtful design, product longevity, and resource efficiency. Pile to pile inventory management serves as the backbone of this model, as it facilitates the reuse and recycling of materials, thus reducing the need for virgin resources. By tracking and managing these materials effectively, businesses can close the loop on production, achieving a more sustainable approach to inventory.
However, implementing pile to pile systems is no easy task. It requires a deep rethinking of supply chain processes, from sourcing and production to distribution and disposal.
The Key Inventory Challenges in the Circular Economy
Managing Complex Material Flows
One of the biggest challenges of pile to pile inventory management is handling complex material flows. Unlike traditional supply chains, where goods move in one direction - from manufacturer to consumer - circular supply chains operate bidirectionally. Materials flow back from the consumer to the producer for reuse, recycling, or refurbishment. This requires robust tracking systems that can monitor where materials are located, their condition, and how they can be reintegrated into production.
In traditional inventory systems, companies typically focus on new products, but in pile to pile inventory management, businesses must handle both new and recovered materials simultaneously. This increases the complexity of inventory tracking, storage, and processing.
Balancing Supply and Demand for Recycled Materials
Another significant challenge is balancing the supply and demand of recycled or reused materials. Often, the availability of recyclable materials does not match the demand for their use in production. Companies must navigate fluctuations in material availability, quality, and cost to maintain an efficient production cycle.
For example, Nike's Reuse-A-Shoe program collects old shoes for recycling into sports surfaces. However, ensuring a consistent supply of worn-out shoes to meet the demand for these surfaces requires sophisticated forecasting and logistics. Balancing this supply and demand cycle is crucial to keeping the operation sustainable and profitable.
Ensuring Material Quality and Consistency
In the pile to pile system, ensuring the consistent quality of reused or recycled materials is another challenge. Many materials, such as plastics, lose their integrity after multiple cycles of recycling, while others require extensive refurbishment before they can be reused in production. Managing the quality of these materials and determining the number of times they can re-enter the production cycle is essential for ensuring product reliability.
For example, in the electronics industry, manufacturers such as Dell and HP have implemented take-back programs to recover used parts. However, not all recovered components meet the quality standards for reuse. Effective pile to pile management involves categorizing these materials, determining which can be reused, and finding alternative solutions for those that can no longer be part of the closed-loop process.
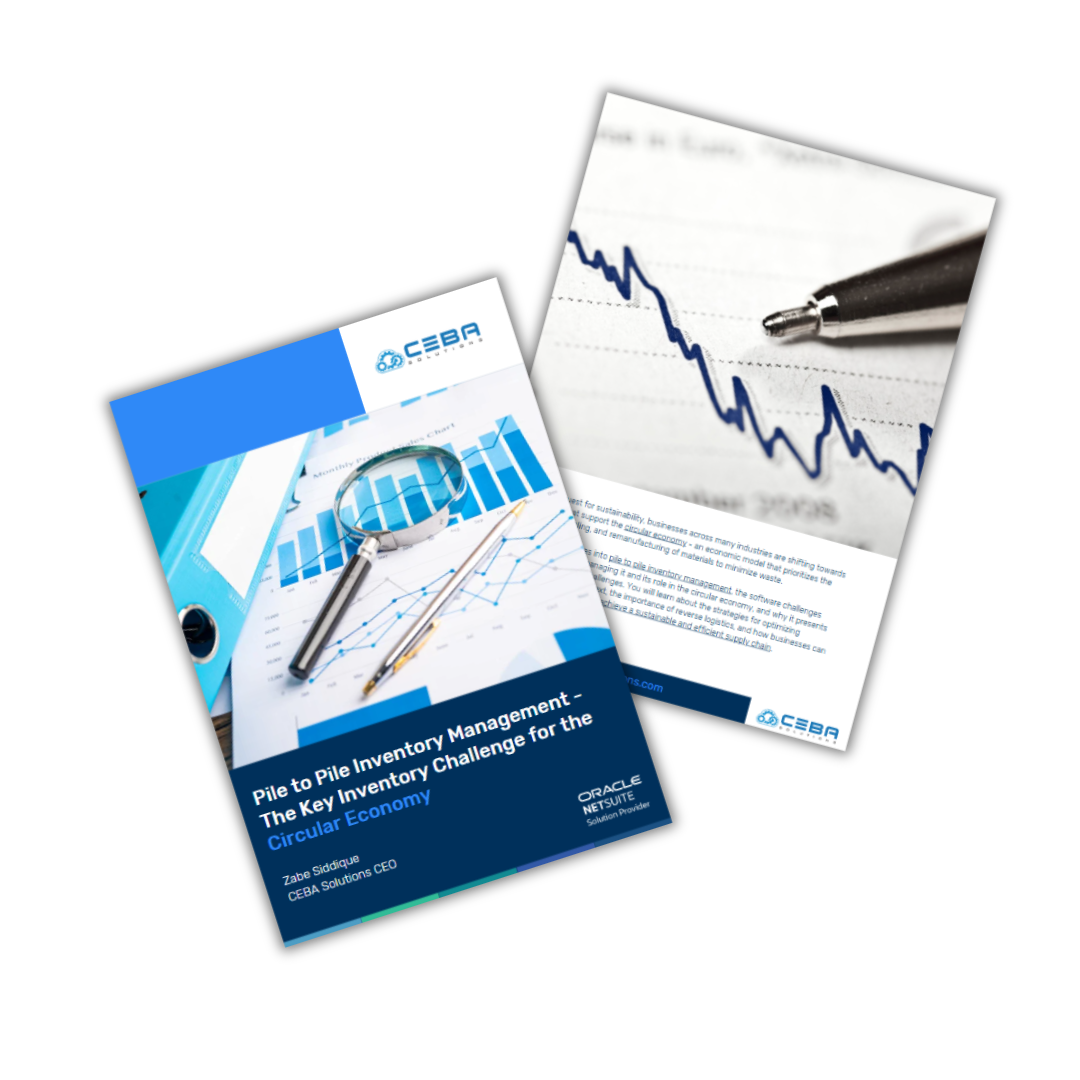
Pile to Pile Inventory Management - The Key Inventory Challenge for the Circular Economy
Download Here!
The Importance of Sustainable Supply Chains and Inventory Optimization
Optimizing Inventory for Circular Supply Chains
Inventory optimization in a pile to pile management system goes beyond simply balancing stock levels for new products. It requires a more dynamic approach that takes into account the flow of recycled, refurbished, and remanufactured goods. This is where advanced data analytics, forecasting, and demand planning come into play. Businesses need to anticipate material flows not just for sales, but for returns, recycling, and remanufacturing as well.
The challenge here lies in predicting not only customer demand but also the rate at which products will be returned or recycled. This makes traditional inventory optimization tools insufficient for the task. Instead, businesses need advanced inventory management software that integrates AI and machine learning to predict material flows accurately and ensure a steady balance between supply and demand.
Case Study: Patagonia and Circular Inventory
Patagonia, the outdoor clothing retailer, offers an example of how pile to pile inventory management can work in practice. Through their Worn Wear program, they collect used clothing from customers, refurbish it, and resell it as second-hand products. Patagonia has developed an efficient system to collect, sort, and repair these items, minimizing waste and promoting sustainability.
However, the logistics of refurbishing used items and keeping them in circulation require sophisticated inventory management. Patagonia must balance the flow of used and new products while ensuring that their refurbished items meet the same quality standards as their new clothing. This type of inventory optimization is key to making their circular model both environmentally sustainable and commercially viable.
"Adopting circular economy practices like pile-to-pile inventory management challenges traditional supply chains, yet it is essential for minimizing waste, optimizing resources, and achieving sustainability targets in today’s business landscape." - Zabe Siddique, CEO - CEBA Solutions
Reverse Logistics as a Pillar of Pile to Pile Inventory Management
What is Reverse Logistics?
Reverse logistics refers to the process of moving goods back through the supply chain, typically for the purpose of reuse, recycling, or disposal. In the context of pile to pile inventory management, reverse logistics is essential for capturing value from returned or end-of-life products. It involves the transportation, warehousing, and handling of materials after their initial use, facilitating their re-entry into the production process.
The efficiency of reverse logistics directly impacts the success of pile to pile inventory management. Without an effective reverse logistics system, businesses cannot efficiently recover materials, which leads to increased waste and reduced sustainability.
Challenges in Implementing Reverse Logistics
Building an efficient reverse logistics system comes with its own set of challenges. It requires coordination between numerous stakeholders, including customers, manufacturers, and logistics providers. Additionally, businesses must develop systems to handle the inspection, sorting, and processing of returned goods.
Reverse logistics also often requires separate infrastructure, which can be costly to set up. Companies may need to establish dedicated recycling or refurbishing centers, employ skilled labor for material assessment, and invest in transportation solutions that support a circular supply chain.
Innovations in Reverse Logistics
Fortunately, advancements in technology are helping to overcome these challenges. Solutions such as blockchain technology are being tested to improve traceability in reverse logistics, ensuring that materials are tracked and handled efficiently as they move back through the supply chain. By leveraging blockchain, companies can guarantee transparency and maintain detailed records of where materials come from, how they are processed, and where they are headed next.
Another example is the use of robotic automation in sorting facilities, which speeds up the process of handling returned goods, improves accuracy, and reduces costs associated with manual labor. These innovations are crucial for making reverse logistics systems both effective and scalable.
How Pile to Pile Management Drives Business Growth and Sustainability
Environmental and Economic Benefits
Pile to pile inventory management offers significant environmental and economic benefits. By reducing the reliance on virgin materials, businesses lower their carbon footprint and decrease the environmental impact of their operations. Simultaneously, reusing materials leads to cost savings by reducing expenses related to raw material procurement and waste disposal.
For instance, Apple has made strides in reducing e-waste through its recycling program, which retrieves old iPhones and extracts valuable components for reuse. By recycling materials, Apple not only contributes to environmental sustainability but also cuts down on production costs.
Strengthening Brand Loyalty and Consumer Trust
Consumers today are increasingly concerned about the sustainability of the products they purchase. By adopting pile to pile inventory management practices and championing circular economy principles, businesses can strengthen their brand image, build consumer trust, and foster brand loyalty. Customers are more likely to engage with brands that demonstrate a commitment to sustainability and ethical practices.
For example, IKEA’s efforts to build a circular business model include offering buy-back programs, where customers can return their old furniture in exchange for store credit. This approach enhances customer loyalty while contributing to the company's sustainability goals.
Final Thoughts
Pile to pile inventory management is an essential practice for businesses transitioning to a circular economy. While it poses unique challenges in managing material flows, ensuring quality, and implementing reverse logistics, it is also key to driving sustainability and business growth. As companies continue to innovate and adopt more sustainable supply chain models, mastering pile to pile inventory management will become increasingly critical.
By optimizing inventory processes, leveraging advanced technologies, and building strong reverse logistics systems, businesses can achieve a more sustainable future—one where materials are continually cycled back into production, waste is minimized, and profitability thrives alongside environmental stewardship.
Key Takeaways
- Pile to pile inventory management is the foundation of sustainable supply chains in a circular economy.
- Businesses face challenges in balancing supply and demand, managing material quality, and implementing reverse logistics, but technological advancements can help.
- Companies like Patagonia and Apple demonstrate the value of circular inventory systems